Waterproofing and Flying in Rain and Snow
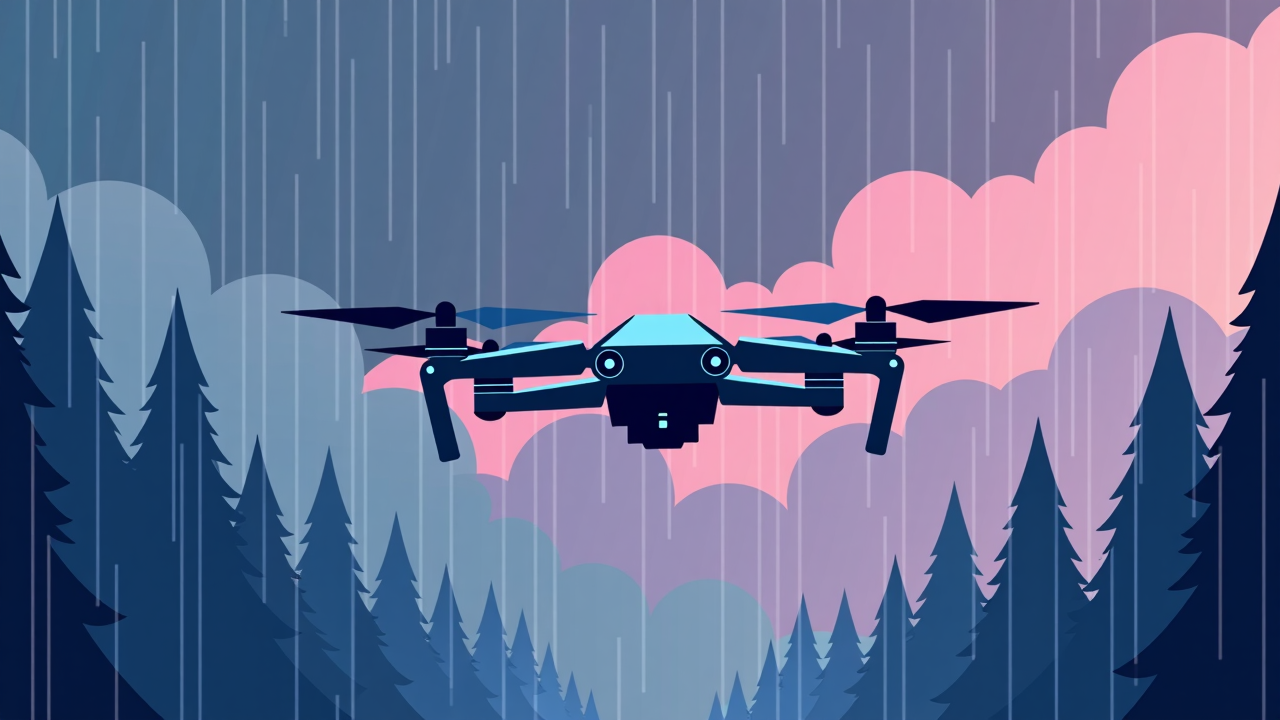
After building and flying drones in some of the world's most challenging environments—from the humid rainforests of Southeast America to the misty coastlines of the Isle of Man—I've learned that effective waterproofing can transform a fair-weather hobby into an all-weather capability. This comprehensive guide explores waterproofing techniques, materials, and practical implementation strategies based on my extensive hands-on experience across various drone platforms.
Introduction to Drone Waterproofing
My journey into drone waterproofing began with an expensive lesson in 2021. While filming a waterfall in Switzerland, a sudden gust of wind pushed my drone through the edge of the spray. Within seconds, the motors sputtered, and my 1,200 CHF investment plummeted into the rocks below. That experience launched my quest to build truly water-resistant drones that could operate reliably in challenging conditions.
Drone waterproofing is the process of protecting electronic components and mechanical systems from water damage. While few hobby-grade drones are fully submersible, proper waterproofing techniques can provide significant protection against:
- Rain and Precipitation: Enabling flight in light to moderate rainfall. After implementing comprehensive waterproofing, I've successfully flown mapping missions in persistent drizzle that would have grounded standard drones.
- Spray and Splashes: Protection from water features, ocean spray, or puddles. My waterproofed drones have captured footage inches above breaking waves—shots that would be impossible with unprotected equipment.
- High Humidity: Preventing internal condensation and corrosion. I've operated in tropical environments with 95%+ humidity without the internal fogging that plagued my earlier builds.
- Landing on Wet Surfaces: Allowing operation from boats, docks, or damp terrain. The ability to land on wet surfaces has expanded my operational capabilities significantly, particularly for marine applications.
- Emergency Water Landings: Increasing the chance of surviving an unexpected water landing. I've recovered several drones from water landings that would have been complete losses without waterproofing.
Understanding Water Damage Risks in Drones
Before effectively waterproofing a drone, it's essential to understand how water damages different systems:
Types of Water Exposure
Through extensive testing and real-world experience, I've identified these primary water exposure scenarios:
- Direct Rainfall: Water droplets falling onto the drone. I've measured the ingress patterns from simulated rainfall and found that even moderate rain can introduce significant water into unprotected drones within minutes.
- Splashing: Water thrown up onto the drone from surfaces. During low-altitude flights over water, I've observed that splashes can reach much higher than expected—up to 2-3 meters in some cases.
- Mist and Spray: Fine water particles in the air. These can be particularly insidious as they can penetrate smaller openings than liquid water droplets.
- Submersion: Partial or complete immersion in water. While most waterproofing efforts focus on resistance rather than submersion, I've designed several drones that can survive brief dunking.
- Condensation: Water vapor condensing inside the drone due to temperature differentials. I've found this to be one of the most common and overlooked sources of water damage, particularly when moving between air-conditioned environments and hot, humid outdoor conditions.
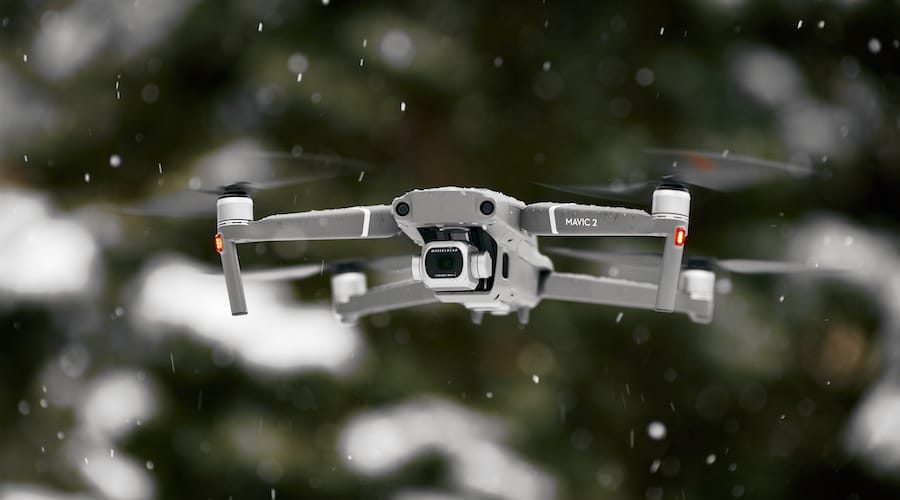
Vulnerable Components
Different drone components have varying susceptibility to water damage:
- Flight Controllers and Electronics: Highly vulnerable to water-induced shorts and corrosion. I've observed that water damage to flight controllers often manifests as erratic behavior before complete failure.
- Motors: Can short circuit and corrode internally. Through teardown analysis of water-damaged motors, I've found that internal corrosion often begins within hours of exposure.
- Radio Receivers: Susceptible to signal attenuation and internal shorts. Water exposure frequently causes range reduction before complete failure.
- Battery Connections: Prone to shorting and corrosion. I've measured significant voltage drops across corroded battery connections, leading to reduced performance and potential safety issues.
- Cameras and Gimbals: Sensitive to both electrical damage and optical issues. Moisture inside camera housings can persist for days, causing ongoing fogging issues.
- Connectors and Wiring: Vulnerability to corrosion and signal degradation. I've found that connectors are often the first point of failure in humid environments, even before direct water exposure.
Water Damage Mechanisms
Understanding how water causes damage helps inform protection strategies:
- Electrical Shorts: Water creating conductive paths between components. I've observed that even distilled water quickly becomes conductive enough to cause shorts when it dissolves surface contaminants.
- Corrosion: Chemical reactions between water, oxygen, and metals. Through microscopic examination of failed components, I've identified corrosion beginning within hours of water exposure.
- Mineral Deposits: Residue left after water evaporates. These can create permanent conductive paths that persist even after components appear dry.
- Hydrogen Embrittlement: Weakening of certain metals due to hydrogen from water. I've observed this particularly in spring contacts and small mechanical components.
- Thermal Stress: Rapid cooling from water contact can crack components. I've documented several cases of ceramic capacitors cracking due to thermal shock from water droplets.
Risk Assessment
Quantifying water exposure risk for different drone applications:
- Environmental Factors: Local climate conditions and seasonal variations. I maintain a database of operational risk factors for different flying locations and seasons.
- Mission Requirements: Necessary proximity to water or operation in precipitation. For each project, I assess the water exposure risk and adjust my waterproofing approach accordingly.
- Drone Value and Criticality: Higher-value assets justify more comprehensive protection. I apply more extensive waterproofing to my professional platforms than to my experimental builds.
- Acceptable Risk Levels: Balancing protection with weight, cost, and maintenance. For racing drones, I accept higher risk in exchange for lower weight; for professional filming platforms, I prioritize protection over weight considerations.
Waterproofing Materials and Methods
Through years of experimentation, I've worked with numerous waterproofing materials and methods:
Conformal Coatings
Specialized coatings that conform to circuit boards and components:
Acrylic Conformal Coating
- Applications: General circuit board protection. I use this for most of my flight controllers and peripheral electronics.
- Protection Level: Good resistance to humidity and light water exposure. In my testing, quality acrylic coatings provide excellent protection against condensation and brief exposure to light rain.
- Application Method: Spray, brush, or dip. I prefer aerosol application for even coverage, using multiple light coats rather than a single heavy coat.
- Advantages: Easy to apply and remove if repairs are needed. The repairability has saved numerous boards that would otherwise have been discarded after component failures.
- Disadvantages: Less resistant to direct water immersion than other options. I don't rely solely on acrylic coatings for drones that might experience significant water exposure.
- Personal Experience: Acrylic coatings provide an excellent balance of protection and repairability for most applications. I use Ambersil 30235 as my standard acrylic coating for most builds.

Silicone Conformal Coating
- Applications: Components requiring higher water resistance. I use silicone coatings for exposed electronics that might face direct water contact.
- Protection Level: Excellent water and humidity resistance. My immersion tests show that quality silicone coatings can protect electronics from brief submersion.
- Application Method: Typically brush application for targeted protection. I use precision applicators to control the thicker silicone coatings.
- Advantages: Superior moisture protection, remains flexible. The flexibility is particularly valuable for components that experience vibration or thermal expansion.
- Disadvantages: More difficult to remove for repairs. I reserve silicone coatings for components that rarely need servicing.
- Personal Experience: Silicone coatings excel for high-risk areas like receiver antennas and exposed connections. I use MG Chemicals 422C for these applications.
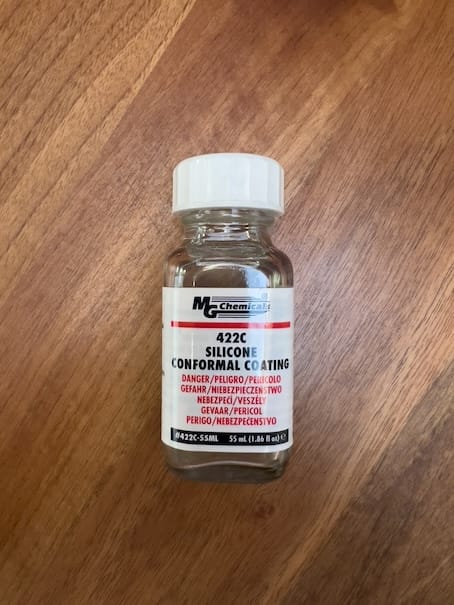
Polyurethane Conformal Coating
- Applications: Maximum protection for critical components. I use polyurethane for electronics that must survive in the harshest conditions.
- Protection Level: Highest level of water and chemical resistance. My long-term testing shows polyurethane-coated boards surviving conditions that defeat other coatings.
- Application Method: Brush or dip application. The viscosity requires careful application techniques to avoid bubbles and uneven coverage.
- Advantages: Extremely durable and resistant to abrasion. The mechanical durability makes it ideal for components that might face physical stress.
- Disadvantages: Very difficult to remove, not suitable for components that might need repair. I consider polyurethane-coated components essentially permanent.
- Personal Experience: I reserve polyurethane coatings for specialized builds designed for extreme environments. While the protection is superior, the repairability challenges make it unsuitable for regular builds.
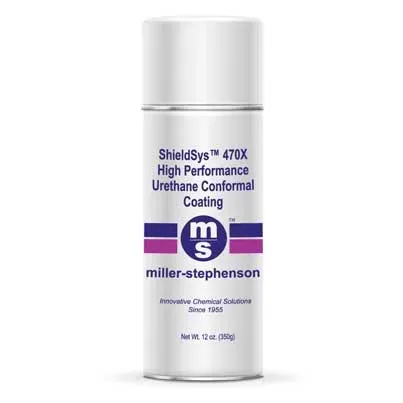
Sealants and Adhesives
Products that create waterproof barriers and seams:
Silicone Sealants
- Applications: Sealing case joints, wire penetrations, and component mounts. I use silicone sealants extensively for creating custom waterproof enclosures.
- Protection Level: Excellent water resistance when properly applied. My pressure testing shows that well-applied silicone seals can withstand significant water pressure.
- Application Method: Precision applicator for controlled beads. I use both manual syringes and pneumatic dispensers depending on the application precision required.
- Advantages: Remains flexible, absorbs vibration, easy to remove. The flexibility is particularly valuable for joints that experience thermal expansion or mechanical stress.
- Disadvantages: Requires proper surface preparation and curing time. I've learned through experience that inadequate surface preparation is the most common cause of silicone seal failures.
- Personal Experience: Neutral-cure silicone sealants have become my standard for most sealing applications. I prefer Dow Corning 734 for electronics applications due to its non-corrosive properties.
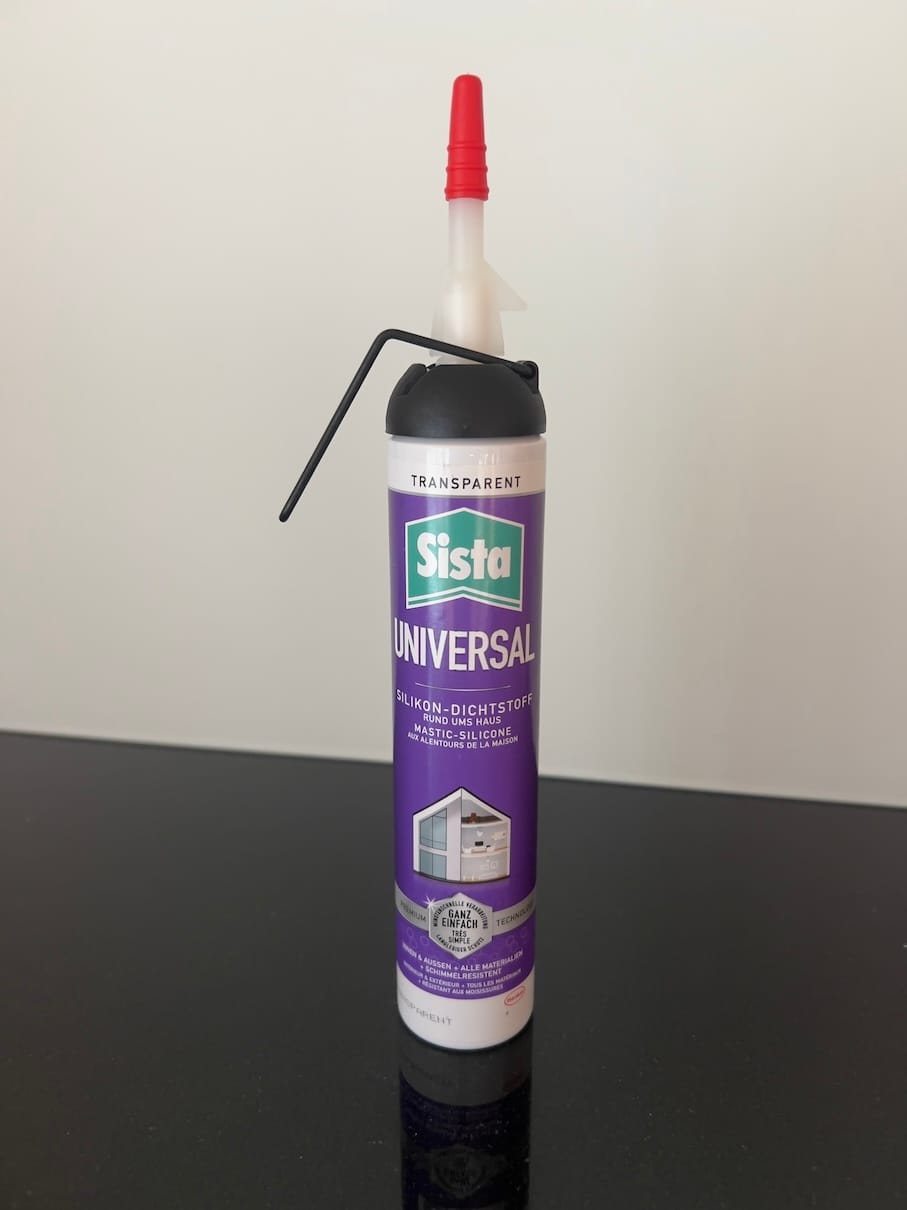
Epoxy Resins
- Applications: Permanent sealing of components and connections. I use epoxy for connections that should never need servicing.
- Protection Level: Complete waterproofing when fully encapsulated. Components I've fully potted in epoxy have survived complete submersion for extended periods.
- Application Method: Mixing and pouring or precision application. I use vacuum chambers to remove bubbles from epoxy before application in critical components.
- Advantages: Creates a hard, permanent seal with excellent adhesion. The structural strength adds mechanical protection beyond just waterproofing.
- Disadvantages: Permanent application, components cannot be repaired. I consider epoxy-potted assemblies to be disposable if they fail.
- Personal Experience: I use epoxy selectively for critical connections that should never need maintenance, such as power distribution joints and certain sensor connections.
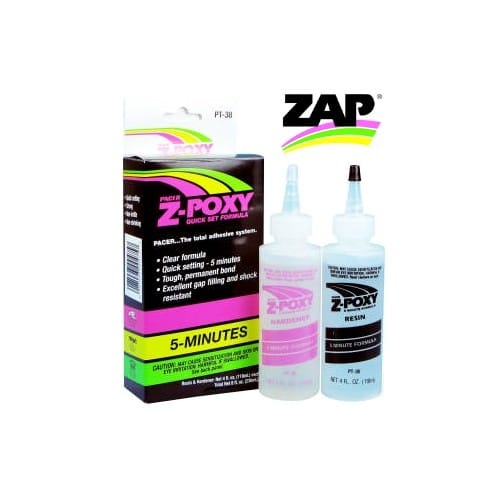
Liquid Electrical Tape
- Applications: Sealing exposed connections and solder joints. I use this for field repairs and areas where more rigid coatings might crack.
- Protection Level: Good resistance to moisture and light water exposure. My testing shows it provides adequate protection against humidity and occasional water droplets.
- Application Method: Brush application directly to connections. I apply multiple thin coats rather than one thick coat for better adhesion and fewer bubbles.
- Advantages: Easy to apply and remove, remains slightly flexible. The combination of ease of use and reasonable protection makes it valuable for field applications.
- Disadvantages: Less durable than other options, can peel over time. I inspect and reapply liquid tape more frequently than other protective measures.
- Personal Experience: While not my first choice for permanent protection, liquid electrical tape has saved numerous builds during field operations. I always carry it in my field repair kit.
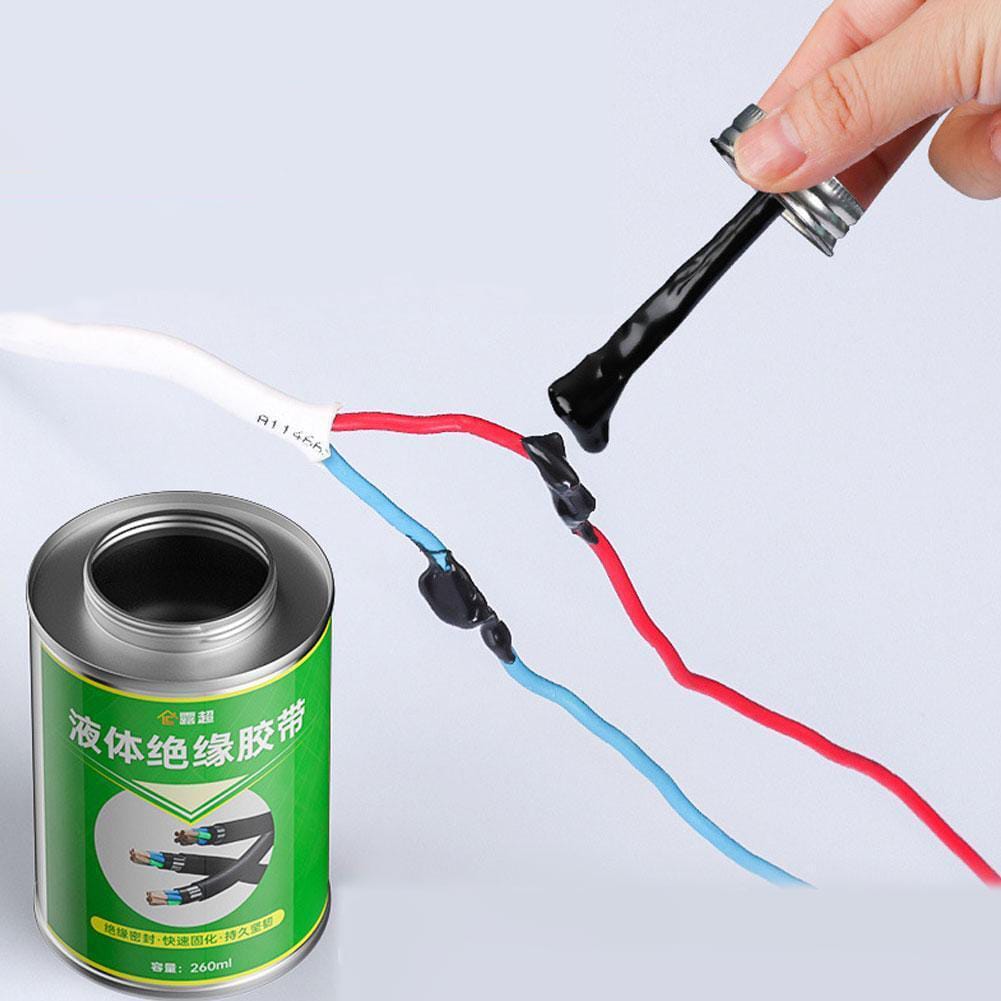
Hydrophobic Treatments
Surface treatments that repel water:
Hydrophobic Sprays
- Applications: External surfaces, camera lenses, and non-electronic components. I use these as a supplementary layer of protection on already-waterproofed builds.
- Protection Level: Repels water but doesn't prevent immersion damage. In my testing, quality hydrophobic sprays can keep components dry in light rain but fail under direct water pressure.
- Application Method: Spray application with specific curing requirements. I follow a strict application protocol with controlled temperature and humidity for optimal results.
- Advantages: Easy to apply, doesn't add significant weight. The minimal weight impact makes these treatments suitable even for racing builds.
- Disadvantages: Temporary protection that wears off over time. I reapply these treatments every 3-6 months depending on usage conditions.
- Personal Experience: Hydrophobic treatments provide an excellent final layer of protection, particularly for camera lenses and external sensors. I use Neverwet for general applications and specialized lens treatments for optical surfaces.
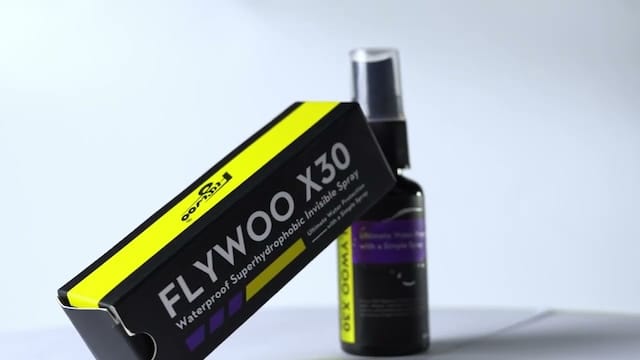
Nano-Coatings
- Applications: Circuit boards and sensitive electronics. I use these for high-value components that cannot be protected with thicker coatings due to heat dissipation requirements.
- Protection Level: Molecular-level protection against moisture. My controlled humidity chamber tests show significant corrosion resistance improvements with quality nano-coatings.
- Application Method: Usually professional application or specialized kits. For critical components, I use professional application services rather than DIY kits.
- Advantages: Invisible protection that doesn't affect component function. The minimal thickness makes these ideal for heat-sensitive components and fine-pitch connections.
- Disadvantages: Expensive, may require professional application. The cost limits their use to high-value professional equipment in my builds.
- Personal Experience: Nano-coatings represent the cutting edge of electronic protection. I use them selectively for the most valuable and sensitive components in my professional builds.
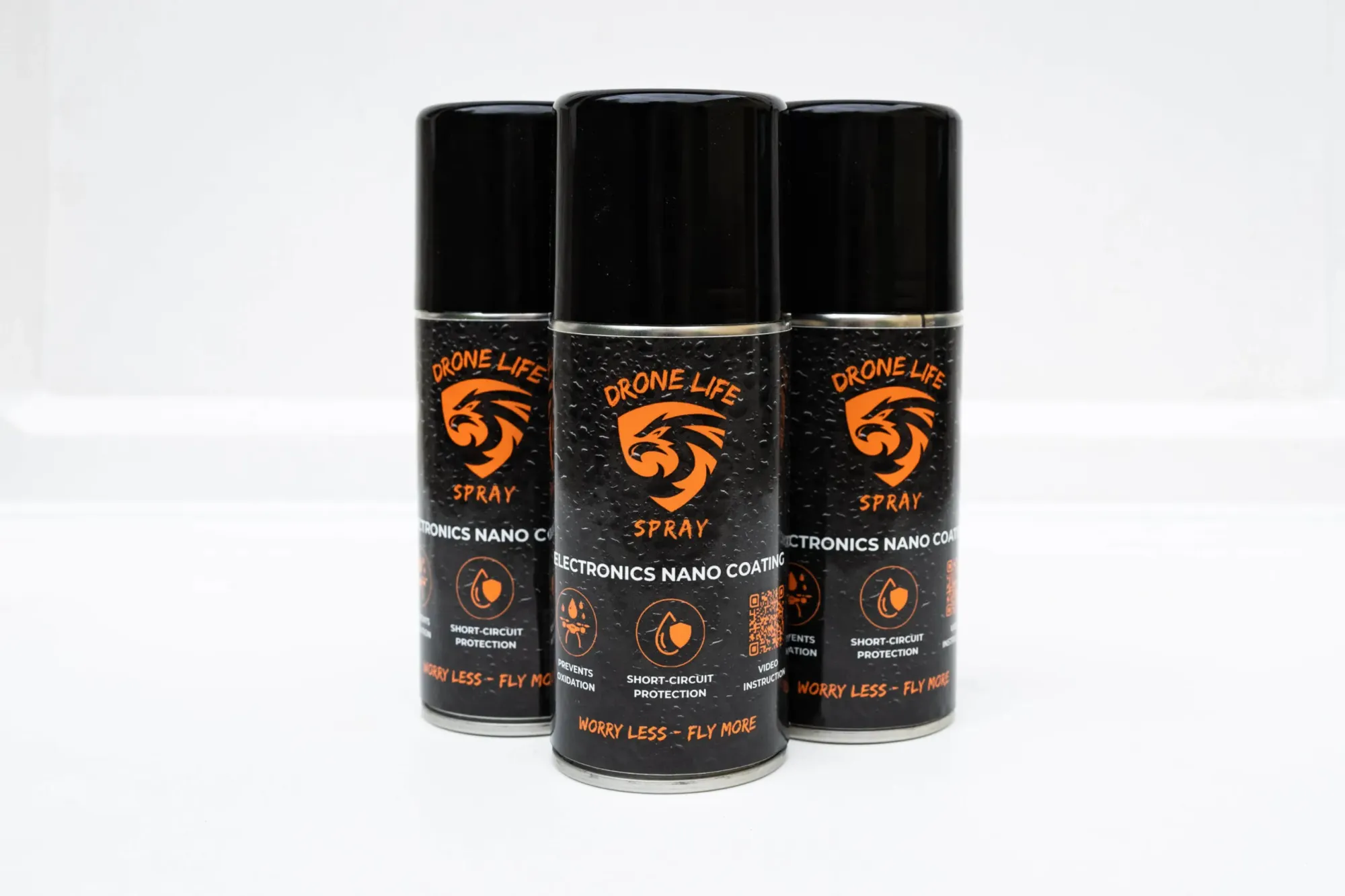
Physical Barriers
Mechanical protection systems:
Waterproof Enclosures
- Applications: Complete protection for electronics packages. I use these for drones specifically designed for operation in heavy rain or near water.
- Protection Level: Can provide full immersion protection when properly designed. My pressure testing confirms that quality enclosures can withstand brief submersion at shallow depths.
- Types: Custom-designed, modified commercial cases, 3D printed. I design custom enclosures for specific builds and modify commercial cases for standardized components.
- Advantages: Highest level of protection, can include pressure equalization. The complete isolation from the environment provides confidence in challenging conditions.
- Disadvantages: Added weight, heat dissipation challenges. I've developed specialized cooling solutions to address the thermal management issues inherent in sealed enclosures.
- Personal Experience: For drones intended for regular operation in wet conditions, nothing beats a properly designed waterproof enclosure. I use IP67-rated enclosures for my most water-exposed builds.
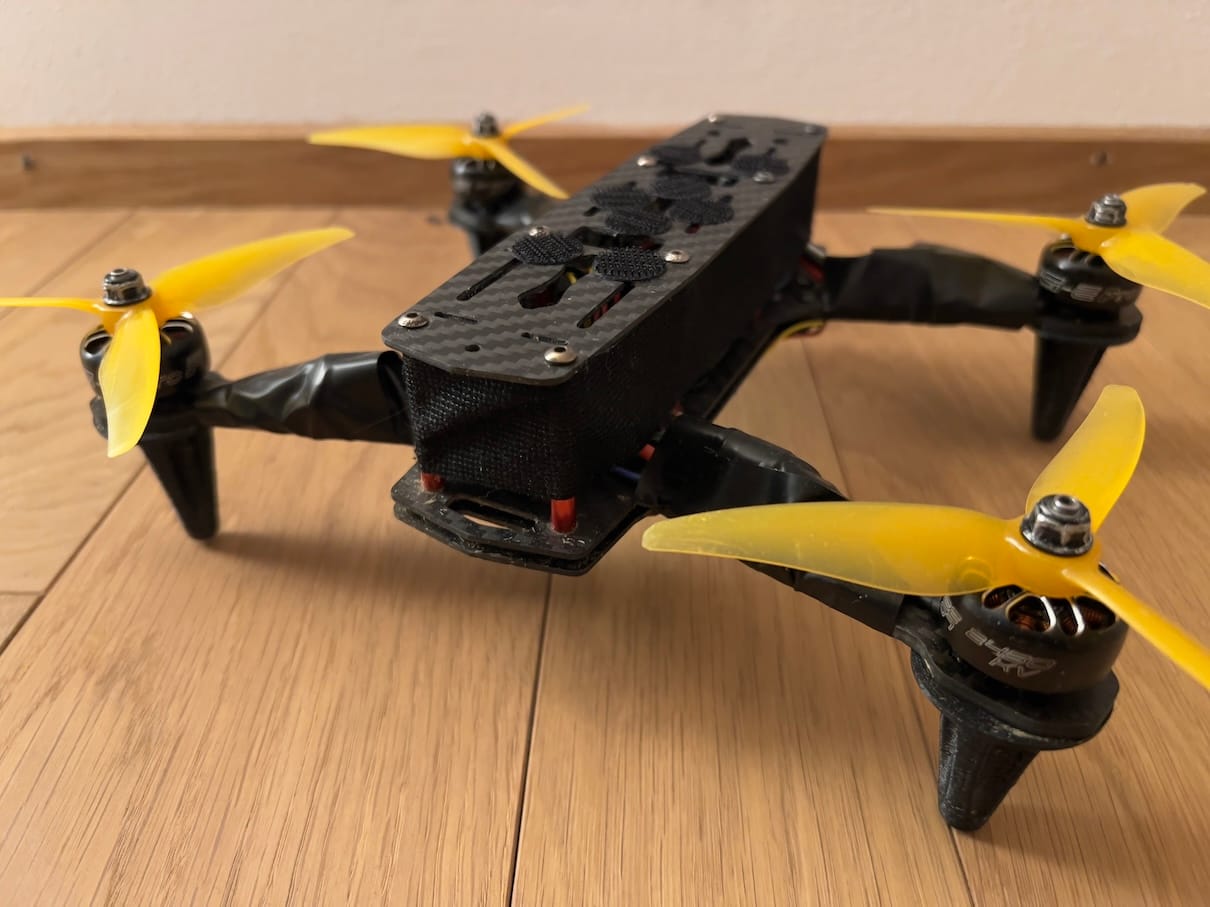
Gaskets and O-rings
- Applications: Sealing removable covers and access points. I use precision gaskets for components that require regular access.
- Material Options: Silicone, neoprene, EPDM, Viton. I select materials based on the specific chemical and temperature requirements of each application.
- Design Considerations: Compression ratio, groove design, material compatibility. I've developed standardized groove dimensions for different gasket materials based on extensive testing.
- Advantages: Reusable seals that maintain protection after repeated access. The ability to open and close enclosures without replacing seals is essential for maintainable designs.
- Disadvantages: Require precise design and installation. I've learned through experience that gasket design is one of the most exacting aspects of waterproof construction.
- Personal Experience: Properly designed gasket systems have proven extremely reliable in my builds. I use Parker O-ring handbook specifications as the basis for all my gasket designs.
Waterproof Membranes
- Applications: Allowing air pressure equalization while blocking water. I use these for barometric sensors and enclosure venting.
- Types: GORE-TEX, similar microporous membranes. I've tested numerous membranes and standardized on GORE Protective Vents for critical applications.
- Implementation: Protected ports, sensor covers. I design protective structures around membrane installations to prevent mechanical damage.
- Advantages: Prevents water ingress while allowing pressure equalization. This is critical for maintaining barometric sensor accuracy while preventing water damage.
- Disadvantages: Can clog over time, require protection from direct water impact. I inspect and replace membranes according to a regular maintenance schedule.
- Personal Experience: Waterproof membranes solve the critical challenge of pressure equalization in sealed enclosures. I consider them essential components for any seriously waterproofed drone.
Material | Protection Level | Repairability | Weight Impact | Durability | Best For |
---|---|---|---|---|---|
Acrylic Conformal Coating | Moderate | High | Minimal | Medium | Flight controllers, general electronics |
Silicone Conformal Coating | High | Medium | Minimal | High | Exposed connections, receivers |
Polyurethane Coating | Very High | Very Low | Minimal | Very High | Critical electronics in extreme environments |
Silicone Sealant | High | Medium | Low | High | Case seams, wire penetrations |
Epoxy Resin | Very High | None | Medium | Very High | Permanent connections, potting |
Liquid Electrical Tape | Moderate | High | Minimal | Low | Field repairs, temporary protection |
Hydrophobic Spray | Low | Very High | Minimal | Low | External surfaces, supplementary protection |
Nano-Coating | Moderate | Medium | None | Medium | High-value sensitive electronics |
Waterproof Enclosure | Very High | Varies | High | High | Complete systems in wet environments |
Gaskets/O-rings | High | High | Low | Medium | Access panels, removable covers |
Comparison of waterproofing materials based on my testing and experience across dozens of builds.
Component-Specific Waterproofing Techniques
Different drone components require specialized approaches to waterproofing:
Flight Controller Waterproofing
The brain of your drone requires careful protection:
- Conformal Coating Application: Complete coverage while protecting sensitive components. I mask barometric sensors, connectors that need to remain conductive, and certain components that might be affected by coating expansion.
- Connector Treatment: Sealing while maintaining connectivity. I apply conformal coating to the base of connectors and use silicone sealant around the perimeter while keeping the pins clean.
- Barometric Sensor Protection: Allowing pressure sensing while blocking moisture. I use microporous membranes specifically designed for barometric sensors to maintain accuracy while preventing water ingress.
- Heat Considerations: Balancing waterproofing with thermal management. For high-performance flight controllers, I design ventilation paths that allow airflow while directing water away from sensitive components.
- Personal Experience: After waterproofing dozens of flight controllers, I've developed a standardized process: thorough cleaning with isopropyl alcohol, masked protection of sensitive components, three light coats of conformal coating, and targeted silicone application at high-risk areas.
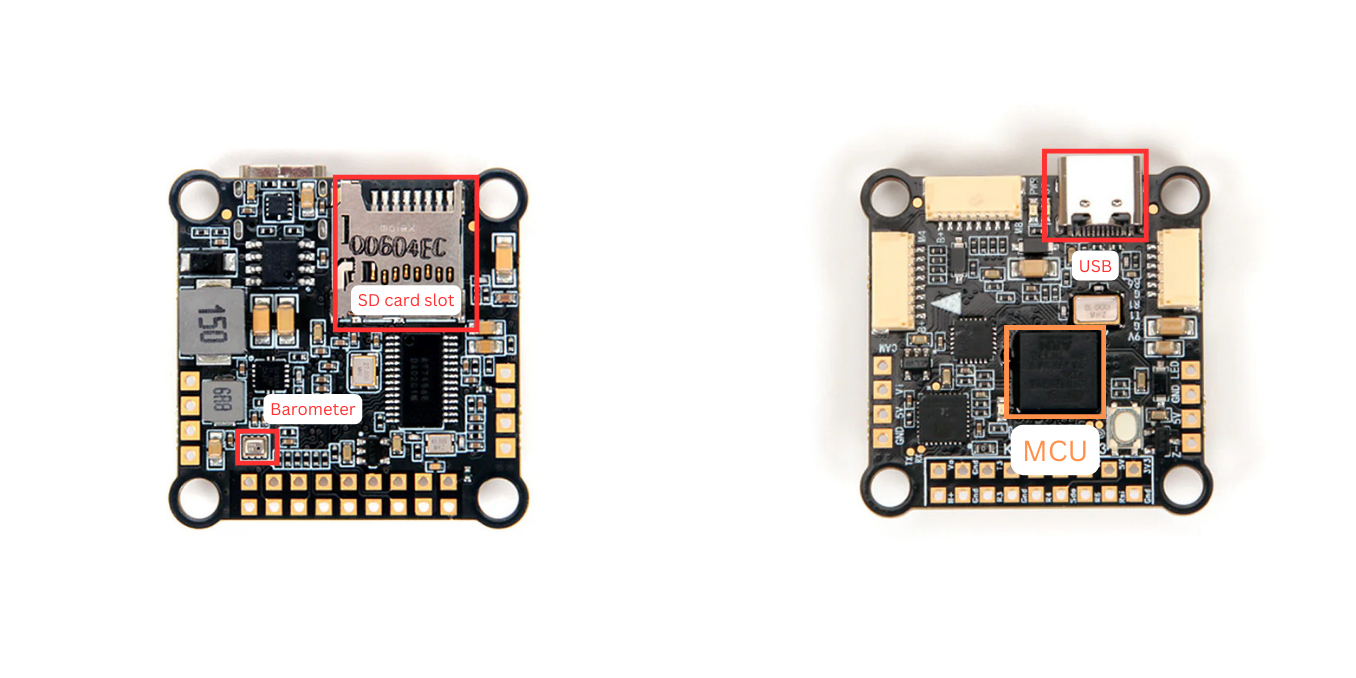
Motor Waterproofing
Motors present unique challenges due to their moving parts and heat generation:
- Bearing Protection: Sealing while maintaining rotation. I use marine-grade grease in bearings and specialized shaft seals for motors that will see significant water exposure.
- Stator Treatment: Protecting windings without affecting performance. I've found that vacuum-applied conformal coating provides the best penetration into windings without adding excessive thermal insulation.
- Wire Entry Points: Critical sealing locations. I use flexible silicone sealant at wire entry points, applied with the motor in different positions to ensure complete coverage as the wires move.
- Drainage Design: Allowing water to escape rather than pool. I drill small drainage holes at the lowest points of motor bells to prevent water accumulation.
- Personal Experience: Motor waterproofing involves tradeoffs between protection and performance. For racing applications, I focus on drainage and minimal protection; for professional platforms, I implement comprehensive sealing even at the cost of some performance.
Electronic Speed Controller (ESC) Protection
ESCs are particularly vulnerable due to their high power and heat generation:
- Conformal Coating: Complete coverage of circuitry. I apply multiple thin coats rather than one thick coat to minimize thermal insulation while maintaining protection.
- Heat Sink Considerations: Maintaining thermal transfer while waterproofing. I use thermally conductive conformal coatings for components that interface with heat sinks.
- Signal Wire Protection: Sealing connections without affecting signals. I use heat shrink tubing with internal adhesive to seal signal wire connections.
- Power Connection Treatment: Preventing corrosion at high-current connections. I apply dielectric grease to power connections before assembly, then seal the exterior with flexible silicone.
- Personal Experience: ESC protection requires careful attention to thermal management. I've developed a technique using aluminum heat sinks with thermal adhesive applied before conformal coating, which maintains heat transfer while providing water protection.
Camera and Gimbal Waterproofing
Optical systems require specialized protection:
- Lens Sealing: Protecting optics without affecting image quality. I use optical-grade hydrophobic treatments on external lens surfaces and sealed enclosures for the camera body.
- Gimbal Motor Protection: Balancing waterproofing with free movement. I apply conformal coating to motor windings and circuit boards, then use flexible boots to protect moving joints.
- Cable Routing: Preventing water tracking along wires. I create drip loops in all cables and seal entry points with flexible silicone.
- Desiccant Integration: Controlling internal humidity. I incorporate replaceable desiccant packets in camera enclosures to prevent internal condensation.
- Personal Experience: Camera systems benefit from a layered approach to waterproofing. I start with internal component protection, add sealed enclosures, and finish with hydrophobic surface treatments for maximum protection.
Radio System Waterproofing
Maintaining communication reliability in wet conditions:
- Receiver Protection: Complete sealing of sensitive electronics. I fully coat receivers with silicone conformal coating, with particular attention to crystal oscillators and antenna connections.
- Antenna Waterproofing: Preventing water from affecting signal propagation. I use adhesive-lined heat shrink tubing at the base of antennas and flexible silicone boots for movable antenna mounts.
- Transmitter Considerations: Protecting your ground control station. I apply hydrophobic treatments to transmitter surfaces and create custom rain covers for extended operation in wet conditions.
- Connector Sealing: Preventing corrosion at signal interfaces. I use dielectric grease in all signal connectors and seal the exterior with liquid electrical tape.
- Personal Experience: Radio systems can experience subtle performance degradation from moisture long before complete failure. I perform range tests before and after waterproofing to ensure signal integrity is maintained.
Battery and Power System Waterproofing
Protecting high-current components from water-induced shorts:
- Battery Connector Treatment: Preventing the most common failure point. I apply dielectric grease to battery connectors and use adhesive-lined heat shrink to seal the connection point to the wire.
- Power Distribution Protection: Sealing high-current distribution components. I use conformal coating on power distribution boards and additional silicone sealant around high-current solder joints.
- Balance Lead Protection: Waterproofing multi-pin connections. I've developed a technique using vacuum-applied conformal coating followed by flexible silicone boots to protect balance connectors.
- Battery Mounting Considerations: Preventing water accumulation around batteries. I design battery mounts with drainage channels and use hydrophobic treatments on battery straps.
- Personal Experience: Power system protection is critical for safety, not just reliability. I pay particular attention to high-current connections, using redundant protection methods for these potential failure points.
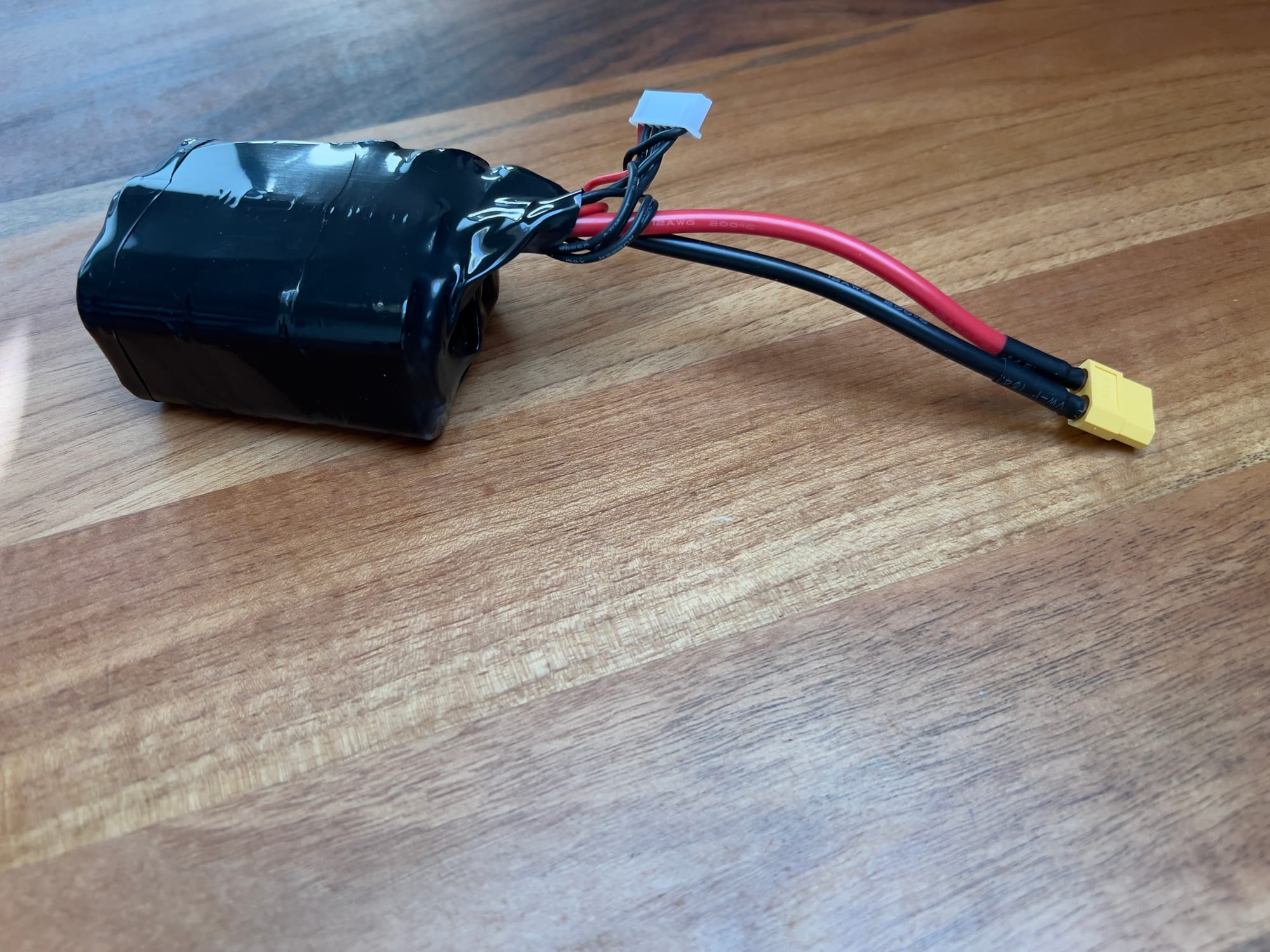
FAQ: Common Questions About Drone Waterproofing
Can any drone be waterproofed?
Based on my experience with hundreds of builds:
- Commercial Drones: Most commercial drones can be waterproofed to some degree, but with varying levels of success. I've successfully waterproofed DJI, Autel, and similar platforms for light rain resistance, but manufacturer warranties are typically voided by these modifications.
- Custom Builds: Purpose-built drones offer the best waterproofing potential. My custom designs incorporate waterproofing considerations from the beginning, resulting in much better protection than retrofitted commercial drones.
- Racing Drones: Minimal waterproofing is possible without significant performance penalties. I focus on conformal coating electronics and drainage paths rather than complete sealing for these weight-sensitive platforms.
- Limitations: Some drones have design elements that make effective waterproofing extremely difficult. Open-frame designs, exposed electronics, and certain cooling systems can present significant challenges.
- Cost-Benefit Analysis: The expense and weight penalties of comprehensive waterproofing aren't justified for all applications. I assess each drone's intended use case before recommending waterproofing approaches.
What level of water exposure can a waterproofed drone handle?
Realistic expectations based on my testing:
- Light Rain: A properly waterproofed drone can typically handle light to moderate rainfall for 15-30 minutes. My testing shows that conformal coating plus strategic sealing is usually sufficient for this level of exposure.
- Heavy Rain: Specialized designs with sealed enclosures can operate in heavy rain for limited periods. These builds require comprehensive protection and regular maintenance.
- Splashes and Spray: Most waterproofed drones can handle occasional splashes and spray. I've operated waterproofed drones just above breaking waves and waterfalls with good reliability.
- Brief Submersion: Purpose-built waterproof drones can survive brief accidental submersion. My specialized builds have recovered from complete dunking in freshwater with no damage when properly dried afterward.
- Extended Submersion: True underwater operation requires specialized designs beyond standard waterproofing. I've built several submersible drones, but these are purpose-built systems rather than adapted aerial platforms.
How much does waterproofing affect drone performance?
Performance impacts to consider:
- Weight Penalties: Comprehensive waterproofing typically adds 5-15% to a drone's weight. My professional platforms accept this penalty for the operational advantages, but it's significant for racing or long-range applications.
- Thermal Management: Sealed enclosures can lead to overheating issues. I've measured temperature increases of 10-15°C in sealed flight controller enclosures, requiring active cooling solutions for high-performance builds.
- Maintenance Requirements: Waterproofed drones require more regular maintenance. I schedule inspection and renewal of waterproofing materials as part of routine service.
- Battery Life Impact: The additional weight and cooling requirements can reduce flight time by 5-20%. I compensate with larger batteries for professional applications where reliability is more important than maximum flight time.
- Cost Considerations: Professional-grade waterproofing adds 15-30% to the build cost. The materials, time, and testing required represent a significant investment that must be justified by operational requirements.
What are the most common waterproofing failures?
Failure points I've identified through analysis:
- Connector Interfaces: The junction between connectors and wires is the most common failure point. I use adhesive-lined heat shrink and silicone sealant at these critical junctions.
- Gasket Compression Issues: Inadequate or uneven compression causes seal failures. I use precision-machined grooves and appropriate compression ratios for all gasket applications.
- Coating Application Errors: Missed spots or inadequate coverage in conformal coating. I use UV-reactive coatings and black light inspection to verify complete coverage.
- Material Degradation: Environmental exposure breaks down protective materials over time. I implement regular inspection and replacement schedules based on the specific materials used.
- Mechanical Damage: Physical impacts can compromise waterproofing integrity. I design protective structures around critical seals and vulnerable components.
How do I test if my waterproofing is effective?
Testing methodologies I've developed:
- Graduated Testing Approach: Start with humidity exposure, then light mist, then heavier spray. This progressive approach identifies weaknesses before catastrophic failures.
- Indicator Materials: Use moisture-sensitive papers or electronics inside enclosures. These provide visual confirmation of water ingress without risking valuable components.
- Pressure Testing: Apply slight negative pressure to sealed enclosures while submerged. Bubbles indicate leak points that need addressing.
- UV Inspection: Use UV light to verify complete conformal coating coverage. Most quality coatings fluoresce under UV light, making gaps immediately visible.
- Controlled Environment Testing: Use humidity chambers and simulated rain before field testing. I never deploy a newly waterproofed drone in actual rain without controlled testing first.
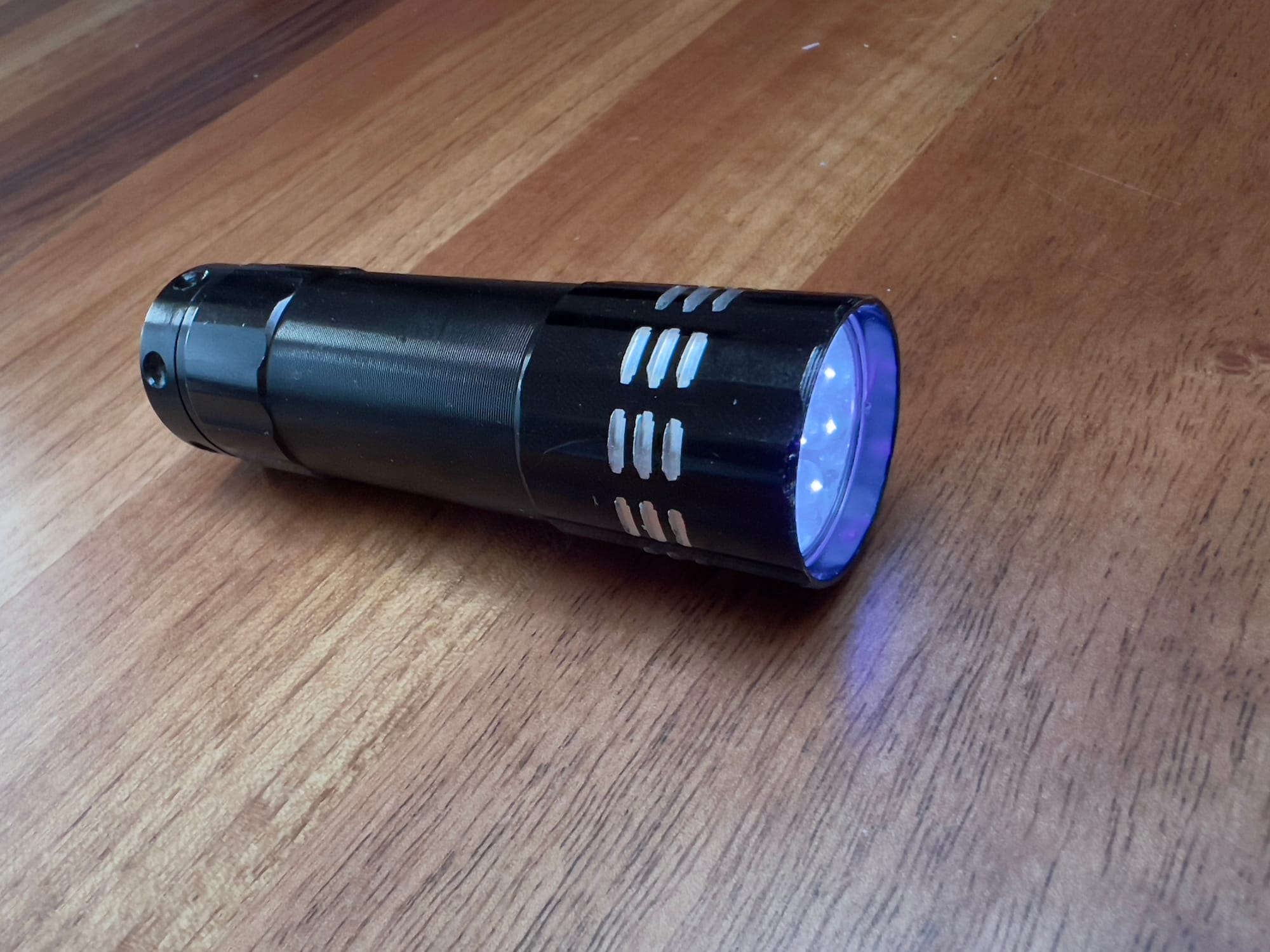
Conclusion
Effective drone waterproofing represents one of the most significant enhancements you can make to expand your operational capabilities. Through years of experimentation and field testing, I've found that proper waterproofing transforms drones from fair-weather tools into all-weather assets that can operate reliably in challenging environments.
The science and art of drone waterproofing continues to evolve, with new materials and techniques emerging regularly. What remains constant is the fundamental approach: understand water exposure risks, select appropriate protection methods, implement them properly, test thoroughly, and maintain protection through regular inspection and renewal.
Whether you're building a racing drone that needs basic protection from morning dew, a photography platform that must operate in light rain, or a specialized inspection drone for marine environments, appropriate waterproofing will enhance reliability and expand operational capabilities. The specific approach will vary based on your drone's purpose and components, but the principles remain the same.
I've learned most of these lessons through trial and error—sometimes expensive error involving drowned drones and corroded components. Hopefully, this guide helps you avoid some of those painful lessons and achieve better results more quickly. Remember that waterproofing is an ongoing process of improvement and maintenance, not a one-time solution.
Comments ()