Drone Motors: Selection, Performance, and Optimization
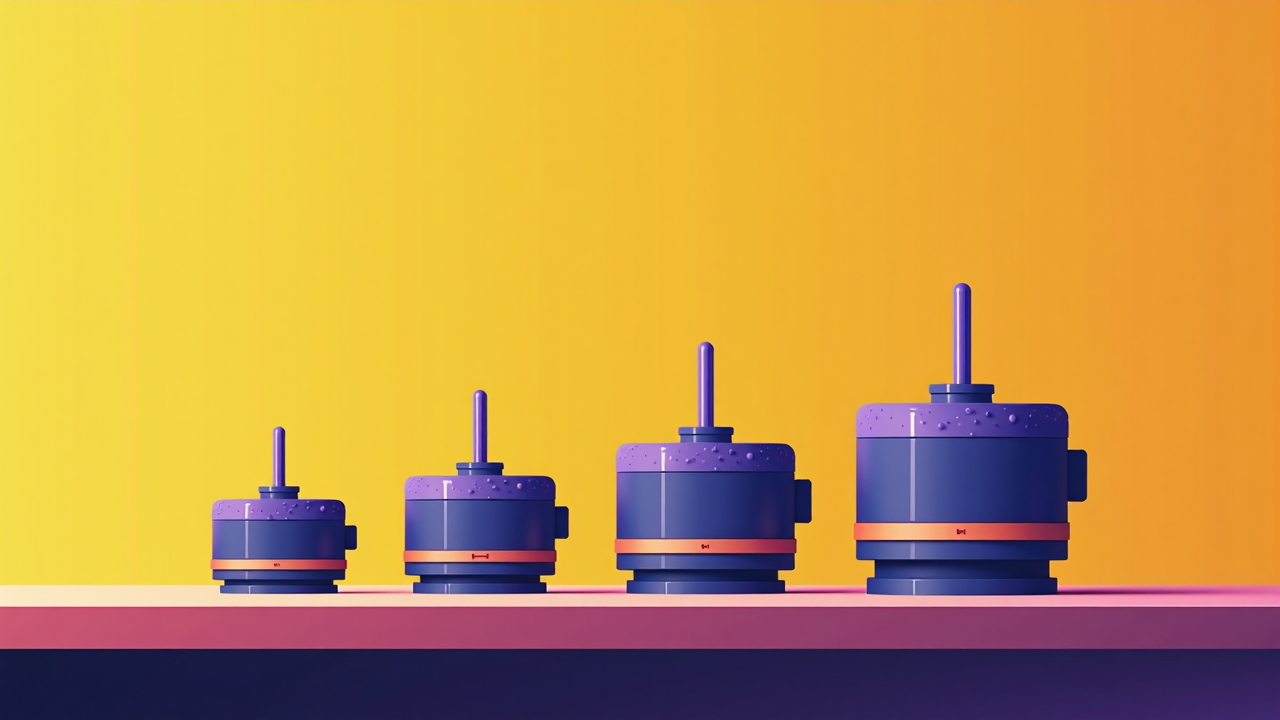
Motors are the beating heart of any FPV drone, directly influencing everything from flight time and agility to top speed and handling characteristics. After building hundreds of drones and testing countless motor combinations over the years, I've learned that motor selection is both an art and a science—one that can make or break your flying experience. This comprehensive guide will walk you through everything you need to know about FPV drone motors, from basic principles to advanced optimization techniques.
Introduction to FPV Drone Motors
FPV (First Person View) drones rely on electric brushless motors to generate the thrust needed for flight. These motors convert electrical energy from your battery into mechanical rotation, which drives your propellers to create lift and maneuverability.
The motors you choose will fundamentally define your drone's character:
- Power and thrust determine your acceleration and top speed
- Weight affects agility and flight time
- Response rate influences handling precision and control
- Efficiency impacts battery life and flight duration
- Durability determines how well they survive crashes and hard landings
Whether you're building your first drone or optimizing your tenth racing rig, understanding motor technology is essential for creating a setup that matches your flying goals.
History and Evolution of Drone Motors
The development of motors for drones represents a fascinating journey of technological innovation that has enabled the modern FPV hobby as we know it today.
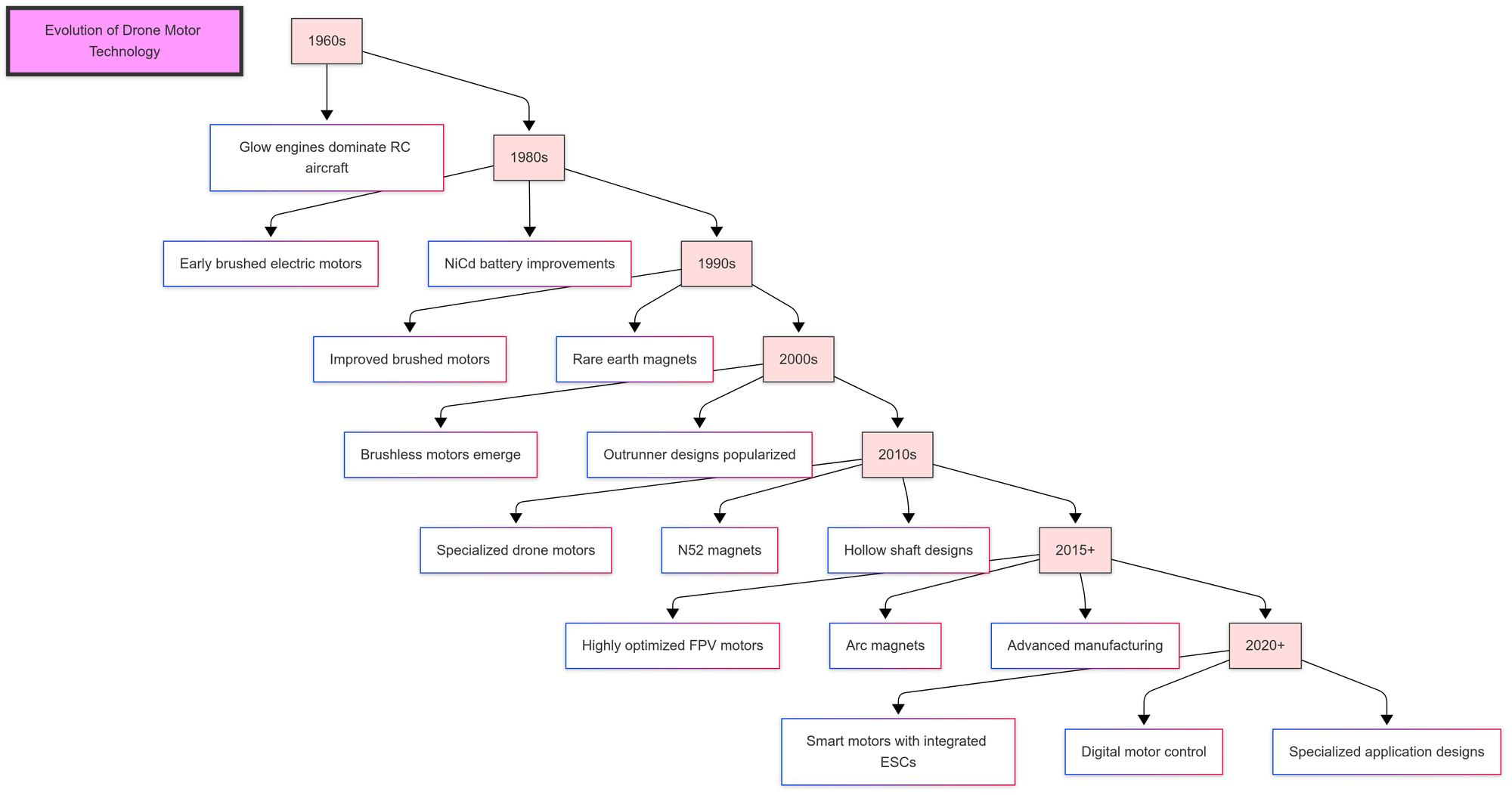
Early RC Motors (1960s-1990s)
The earliest radio-controlled aircraft used glow engines (miniature internal combustion engines) or brushed electric motors:
- 1960s-1970s: Glow engines dominated RC aircraft, with limited electric options
- 1980s: Early brushed motors became more viable with NiCd battery improvements
- 1990s: Higher-quality brushed motors with rare earth magnets improved performance
These early electric systems were heavy, inefficient, and limited in power, making true acrobatic flight difficult.
Brushless Revolution (2000s)
The early 2000s saw the emergence of brushless motors for RC applications:
- 2000-2005: First commercially viable brushless motors and ESCs
- 2005-2010: Outrunner designs (where the bell rotates around the stator) became popular for their higher torque
- 2007-2010: RC helicopters drove innovation in motor design and control
These early brushless motors were primarily designed for fixed-wing aircraft and helicopters, not the multirotor drones we know today.
The Multirotor Era (2010-2015)
The explosion of multirotor drones created demand for specialized motors:
- 2010-2012: First generation of dedicated multirotor motors (large, heavy designs)
- 2012-2013: Introduction of the common "22XX" size format
- 2013-2014: Improved manufacturing techniques reduced weight
- 2014-2015: N52 magnets became standard, significantly improving power density
I have seen some "high-performance" motors from this era—they were considered powerful at the time but would be laughably heavy and underpowered by today's standards.
Modern FPV Motor Development (2015-Present)
The past several years have seen rapid advancement in motor technology specifically for FPV applications:
- 2015-2017: Specialized racing motors with lightweight designs
- 2017-2018: Introduction of titanium shafts and advanced bell designs
- 2018-2019: Arc magnets and optimized air gaps for efficiency
- 2019-2020: Ultra-lightweight designs with improved durability
- 2020-Present: Smart motors with integrated ESCs and digital control systems
The rate of innovation has been remarkable—motors have simultaneously become lighter, more powerful, more efficient, and more durable over a relatively short period.
Fundamentals of Brushless Motors
Brushless vs. Brushed Motors
Early RC aircraft used brushed motors, which have physical brushes that make contact with a commutator to create rotation. While simple and inexpensive, these motors suffer from:
- Lower efficiency
- Reduced lifespan due to brush wear
- Limited power density
- Higher maintenance requirements
Modern FPV drones use brushless DC (BLDC) motors, which eliminate physical brushes in favor of electronic commutation. This advancement brings:
- Higher efficiency (80-90% vs. 50-60% for brushed)
- Longer lifespan (no brushes to wear out)
- Better power-to-weight ratio
- Improved heat dissipation
- Lower maintenance requirements

Brushless Motor Components
Understanding the physical components of a brushless motor helps in evaluating quality and suitability for different applications:
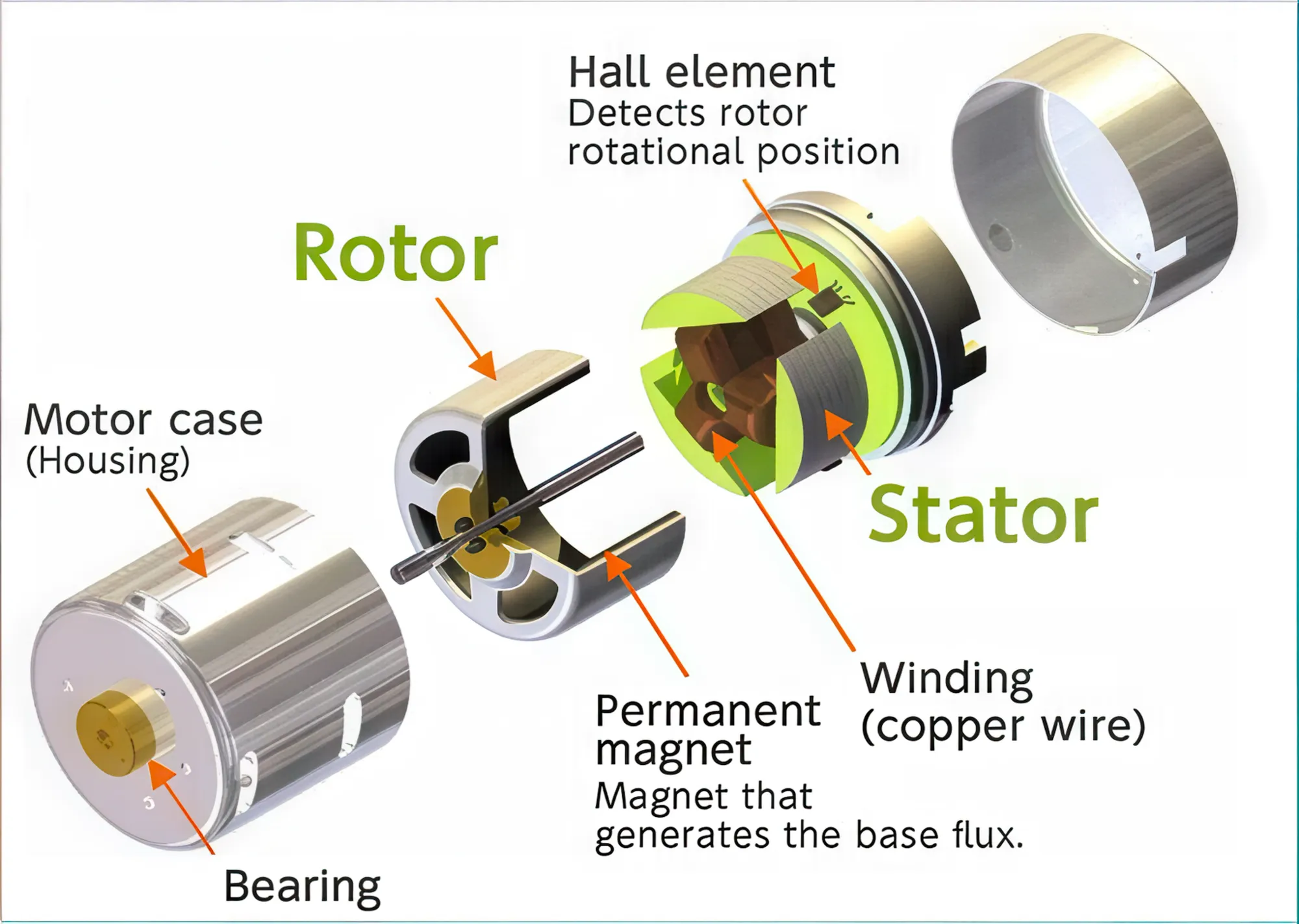
- Bell (Rotor): The outer rotating part that holds the magnets and attaches to the propeller.
- Stator: The stationary inner core with wrapped copper windings. The stator's size is a key specification (more on this later).
- Magnets: Typically made from neodymium alloys (N52, N54, etc.), these create the magnetic field that interacts with the stator windings.
- Windings: Copper wire wrapped around the stator poles in specific patterns (Delta or Wye configuration).
- Bearings: Support the rotating bell and reduce friction. Quality bearings are crucial for longevity and performance.
- Motor Shaft: Connects the bell to the bearings and extends to mount the propeller.
- Base/Mount: The bottom portion with mounting holes to attach the motor to your drone frame.
How Brushless Motors Work
Brushless motors operate on electromagnetic principles:
- The ESC (Electronic Speed Controller) sends precisely timed electrical pulses to the motor windings
- These pulses create electromagnetic fields in the stator
- The electromagnetic fields interact with the permanent magnets in the bell
- This interaction creates rotational force (torque)
- The ESC continuously adjusts the timing and strength of these pulses to control speed and direction
This electronic commutation is what makes brushless motors so efficient and responsive. When I'm pushing through a tight technical track, I can feel the immediate response from a quality motor/ESC combination—there's virtually no delay between stick input and motor reaction.
Understanding Motor Specifications
Deciphering motor specifications is essential for making informed choices. Let's break down the key parameters:
Motor Size Designation
FPV motors are typically labeled with a four-digit number, such as 2207 or 2306. This notation tells you the physical dimensions of the stator:
- First two digits: Stator width (diameter) in mm
- Last two digits: Stator height in mm
For example, a 2207 motor has a stator that is 22mm wide and 7mm tall.
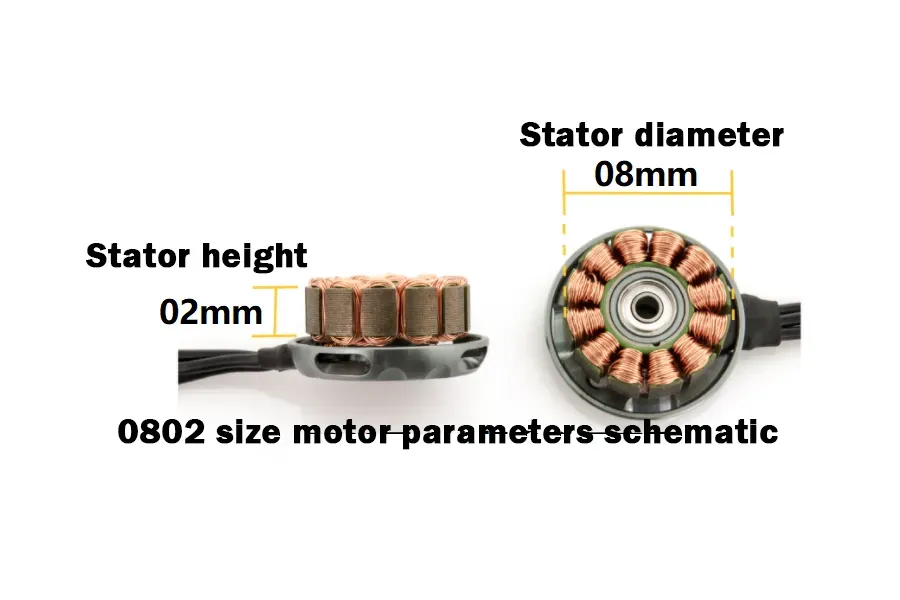
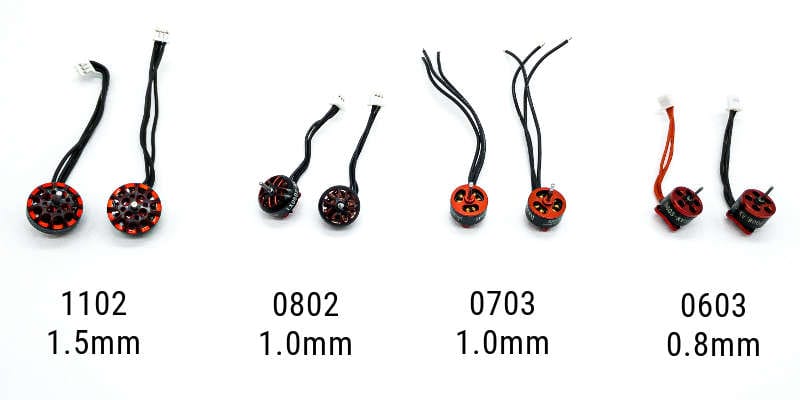
Generally:
- Larger stator width = more torque
- Taller stator height = more power and top-end performance\
In my experience, the difference between a 22mm and a 23mm stator width might seem small on paper, but can completely transform how a drone feels in flight. My 2207 freestyle build has noticeably more snappy response than my otherwise identical 2306 setup, which feels more smooth and linear in power delivery.
KV Rating
KV (Kilo-Velocity) represents the theoretical RPM (revolutions per minute) the motor will turn per volt applied with no load:
- A 2400KV motor on a 4S battery (16.8V fully charged) would theoretically spin at 40,320 RPM (2400 × 16.8) without a propeller
In practice, actual RPM will be lower due to load and inefficiencies. The KV rating has significant implications:
- Higher KV (2400KV+): More top speed, faster response, better suited for racing and smaller props
- Medium KV (1700-2300KV): Balanced performance, good for freestyle and all-around flying
- Lower KV (1300-1600KV): More torque, better efficiency, suited for larger props and long-range flying
One mistake I made early in my FPV journey was always choosing the highest KV motors available, thinking "faster is better." I quickly learned that ultra-high KV motors on a freestyle quad made it twitchy and difficult to fly smoothly, not to mention the drastically reduced flight time.
Stator Size Impact
The stator size directly affects motor performance:
Stator Size | Typical Use Case | Characteristics |
---|---|---|
1105-1306 | Micro quads (2-3") | Lightweight, lower power, efficient |
1407-1506 | Mini quads (3-4") | Good balance of weight and power |
2004-2206 | Mid-size quads (4-5") | Responsive, good for technical flying |
2207-2306 | Standard 5" quads | Powerful all-rounders |
2407-2507 | Heavy freestyle/cinematic | Maximum power, handles heavy payloads |
2807-2912 | 7"+ long range | High torque for large props |
Larger stators can produce more power but add weight. The sweet spot depends on your frame size, battery, and flying style.
Magnet Strength and Types
Magnets are graded by their strength, with higher numbers indicating stronger magnetic force:
- N48: Standard strength
- N52: Strong, common in mid-range motors
- N54/N55: Very strong, found in premium motors
Stronger magnets provide more torque and responsiveness but can reduce efficiency and increase motor temperature. Some manufacturers use arc magnets (curved to match the bell's circumference) rather than traditional straight magnets, claiming improved efficiency.
After burning through several motors with weaker magnets that demagnetized after hard crashes, I've found that investing in motors with N52 or better magnets pays off in longevity, especially for freestyle flying where impacts are inevitable.
Winding Configurations
Motor windings can be arranged in different patterns:
- Delta: Three connections, generally more powerful at higher RPMs
- Wye (Star): Three connections with a center tap, typically more efficient at lower RPMs
Most FPV motors use Delta windings for their performance characteristics, but some manufacturers experiment with hybrid or modified winding patterns for specific performance goals.
Weight Considerations
Motor weight is a critical factor that affects:
- Flight characteristics: Lighter motors mean more agile handling
- All-up weight: Impacts flight time and performance
- Rotational mass: Affects responsiveness to throttle changes
Modern motors have been trending lighter while maintaining power, with premium options using titanium shafts and aluminum/magnesium alloy bells to reduce weight without sacrificing strength.
Power Handling Capabilities
A motor's ability to handle power is typically measured in watts and is determined by:
- Copper mass in the windings
- Heat dissipation capability
- Construction quality
Manufacturers often provide specifications like "max continuous power" and "burst power," though these should be taken as guidelines rather than absolute limits.
I've learned to be skeptical of power claims after watching a supposedly "1200W capable" motor melt down after just 30 seconds at about 800W during a bench test. Quality motors from reputable manufacturers tend to be more conservative in their ratings.
Motor Selection Guide
Choosing the right motors involves matching their characteristics to your specific build and flying goals.
Matching Motors to Frame Size
Frame size largely dictates appropriate motor choices:
Frame Size | Recommended Motor Sizes | Typical KV Range |
---|---|---|
2-3" Micro | 1105-1306 | 3000-6000KV |
3" Toothpick | 1204-1404 | 2800-4500KV |
3.5" Cinewhoop | 1404-1506 | 2600-3600KV |
4" Lightweight | 1606-2004 | 2400-3200KV |
5" Freestyle | 2205-2306 | 1750-2500KV |
5" Racing | 2004-2207 | 2400-2800KV |
6" Freestyle | 2306-2407 | 1600-2000KV |
7"+ Long Range | 2507-2912 | 1300-1700KV |
These are starting points—your specific requirements might call for variations from these recommendations.
Considerations for Different Flying Styles
Different flying styles demand different motor characteristics:
Racing
- Priority: Speed, acceleration, responsiveness
- Recommended: Lower weight, higher KV (2400-2800KV for 5")
- Stator size: Often slightly smaller diameter but taller (e.g., 2207)
- Notes: Racing motors prioritize burst performance over durability and efficiency
I've found that dedicated racing builds benefit from motors with slightly lower weight and inertia, even at the expense of some power. The ability to change direction quickly often matters more than absolute thrust in technical tracks.
Freestyle
- Priority: Smooth power delivery, durability, good throttle resolution
- Recommended: Medium KV (1800-2300KV for 5")
- Stator size: Balanced (e.g., 2306, 2207)
- Notes: Need to handle varied flying from smooth cruising to aggressive maneuvers
For freestyle, I prefer motors with a bit more stator mass that provide smoother throttle response and better handling in both slow precise movements and high-power tricks.
Cinematic/Long Range
- Priority: Efficiency, smooth operation, reliability
- Recommended: Lower KV (1300-1800KV for 5-7")
- Stator size: Often larger for torque with big props (e.g., 2407, 2507)
- Notes: Must balance power needs with efficiency for extended flight times
On my long-range builds, I've found that slightly oversized motors running at lower throttle percentages provide better efficiency than smaller motors running at higher throttle. This counter-intuitive approach has added minutes to my flight times.
Micro Builds
- Priority: Weight savings, adequate power
- Recommended: Higher KV (3000-6000KV depending on size)
- Stator size: As small as possible while meeting power needs
- Notes: Every gram matters; even small weight differences are noticeable
Power-to-Weight Ratios
A useful metric for evaluating motor suitability is the thrust-to-weight ratio of the complete build:
- Racing: 12:1 to 15:1 ratio (extremely responsive, shorter flight times)
- Freestyle: 8:1 to 12:1 ratio (good balance of responsiveness and flight time)
- Cinematic: 5:1 to 8:1 ratio (smoother flying, longer flight times)
- Long Range: 3:1 to 5:1 ratio (maximum efficiency, stable flight)
These ratios represent the total thrust available divided by the all-up weight of the drone.
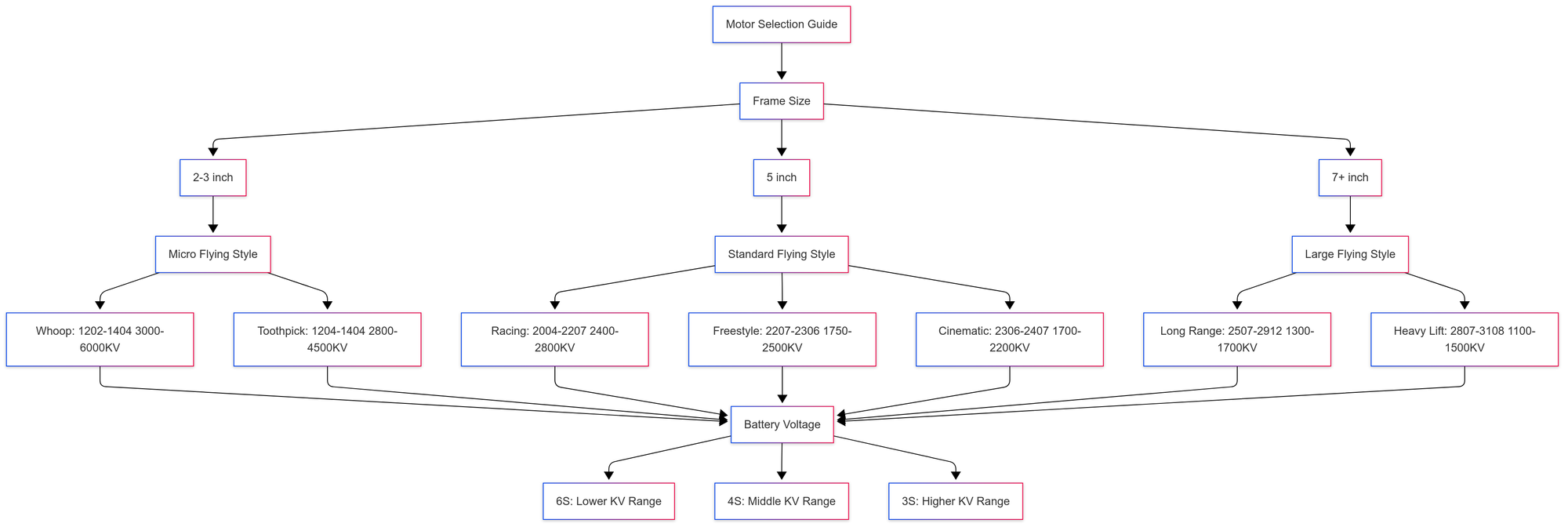
Motor and Prop Matching Principles
Motors and propellers must be matched carefully:
- Larger props require motors with more torque (larger stator diameter)
- Higher pitch props put more load on motors and may require lower KV
- Heavier props increase motor temperature and reduce responsiveness
A general guideline for 5" quads:
- 5x4x3 props (5", 4" pitch, 3 blades): Work well with 2300-2600KV motors
- 5x5x3 props: Better matched with 1900-2300KV motors
- 5x4.5x2 props: Can use higher KV (2400-2800KV) for racing
I once tried running aggressive 5x4.3x3 props on high KV (2750KV) motors on 6S, and while the thrust was incredible, the motors got so hot I could smell them after a 2-minute flight. Proper matching is crucial for longevity.
Battery Voltage Considerations
Motor KV should be matched to your battery voltage:
Battery | KV Range for 5" | Notes |
---|---|---|
3S (12.6V) | 2600-3000KV | Less common now, but still used for some racing builds |
4S (16.8V) | 2300-2600KV | Good balance, popular for freestyle |
5S (21.0V) | 1900-2300KV | Growing in popularity, good power/efficiency balance |
6S (25.2V) | 1700-2000KV | Maximum power, popular for freestyle and cinematic |
Higher voltage systems (6S) with appropriate lower KV motors generally provide:
- Better efficiency
- More consistent power throughout the battery discharge
- Lower current draw for the same power output
- Less voltage sag under load
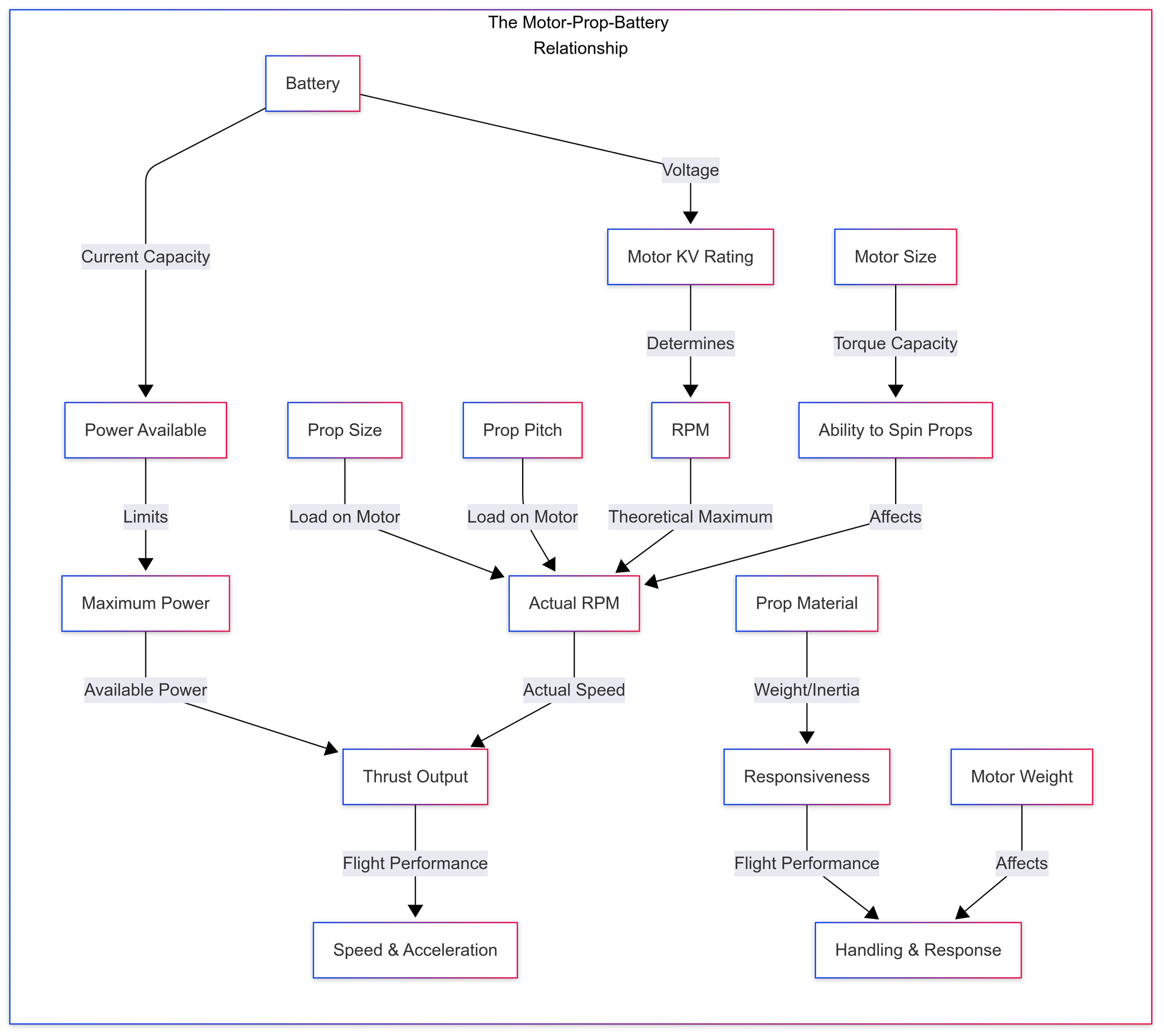
Motor Performance Metrics
Understanding how motors perform requires looking beyond specifications to actual performance data.
Thrust Testing Explained
Thrust tests measure the actual force produced by a motor/prop combination at various throttle levels:
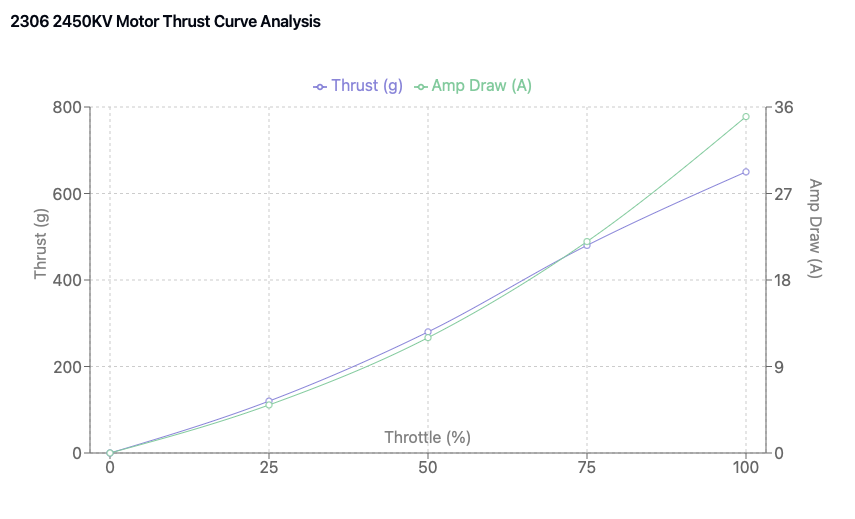
Key metrics from thrust tests include:
- Maximum thrust: Peak force produced at 100% throttle
- Thrust curve: How linearly thrust increases with throttle input
- Efficiency: Thrust produced per watt of power consumed
- Amp draw: Current consumption at different throttle levels
I've built my own thrust testing rig, and the results often contradict manufacturer claims. Some motors advertised as "high thrust" actually produce less force than more modest options but run significantly hotter.
Interpreting Thrust Data Charts
When examining thrust test data:
- Look beyond maximum thrust - A motor that produces slightly less peak thrust but has a more linear thrust curve often provides better handling.
- Consider thrust at typical throttle positions - Most flying happens between 20-60% throttle, so performance in this range matters more than maximum thrust.
- Compare efficiency - Two motors might produce similar thrust, but if one draws significantly less current, it will provide longer flight times.
- Check temperature rise - Excessive heat indicates inefficiency and potential longevity issues.
Efficiency Considerations
Motor efficiency (thrust per watt) varies across the throttle range:
- Most motors are most efficient at 30-60% throttle
- Efficiency drops significantly at very low and very high throttle
- Larger stators tend to be more efficient with larger props
- Higher KV motors typically sacrifice some efficiency for responsiveness
For long-range builds, I prioritize motors that maintain good efficiency in the 30-50% throttle range, as this is where the drone will spend most of its flight time.
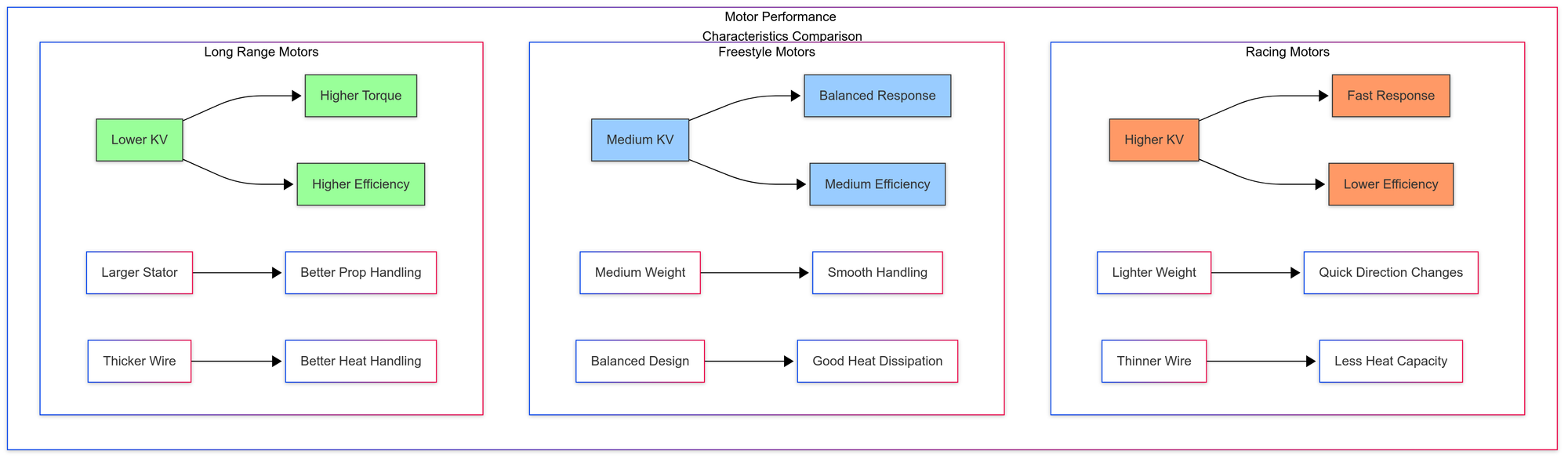
Temperature Management
Motor temperature is a critical indicator of appropriate matching and setup:
- Normal operating temperature: Warm to the touch but not uncomfortable to hold (40-60°C)
- Caution range: Too hot to touch comfortably (60-80°C)
- Danger zone: Too hot to touch at all (80°C+)
Factors affecting motor temperature:
- KV rating (higher KV = more heat)
- Prop size and pitch (more aggressive = more heat)
- Flying style (aggressive maneuvers = more heat)
- Ambient temperature
- Cooling airflow
I've developed a habit of touching my motors after each flight—it's a simple check that has saved me from damaging many motors by alerting me to potential issues before failure.
Noise Characteristics
Motor noise can indicate performance characteristics:
- Smooth, lower-pitched sound: Generally indicates efficient operation
- High-pitched whine: May indicate very high RPM, potentially pushing limits
- Grinding or uneven sound: Could indicate bearing issues or imbalance
- Resonance at certain throttle positions: May indicate vibration issues
Beyond being annoying, excessive noise often correlates with inefficiency and can signal potential problems.
Advanced Motor Concepts
For those looking to optimize performance further, these advanced concepts can help fine-tune motor selection and setup.
Air Gap Optimization
The air gap is the distance between the stator and magnets:
- Smaller gap: More powerful, more responsive, but potentially less efficient
- Larger gap: More efficient, runs cooler, but less powerful
Premium motors often feature precisely optimized air gaps that balance performance and efficiency.
Bearing Types and Quality
Bearings are critical components that affect performance and longevity:
- Standard bearings: Adequate for casual flying
- Sealed bearings: Better protection against dust and moisture
- Ceramic bearings: Reduced friction, longer life, higher cost
- Hybrid bearings: Ceramic balls with steel races, good balance of performance and cost
I've found that upgrading to quality Japanese bearings (even standard steel ones) makes a noticeable difference in motor smoothness and longevity compared to the generic Chinese bearings found in budget motors.
Bell Design and Materials
Bell design affects weight, cooling, and durability:
- Standard bells: Usually aluminum, good balance of weight and strength
- Lightweight bells: Thinner material or cutouts to reduce weight
- Cooling designs: Additional cutouts or fins to improve airflow
- Material variations: Some premium motors use titanium, magnesium alloys, or carbon fiber components
Single-sided vs. Double-sided Flux Designs
Motor designs vary in magnetic flux patterns:
- Single-sided flux: Magnets only on the outer edge of the bell, lighter but less powerful
- Double-sided flux: Magnets on both top and sides of the bell, more powerful but heavier
Double-sided designs are becoming more common in premium motors for their performance advantages, particularly in larger sizes.
Hollow vs. Solid Shaft Designs
Motor shafts come in two main designs:
- Solid shaft: Traditional design, maximum strength
- Hollow shaft: Lighter weight, adequate strength for most applications, better cooling
For racing and freestyle, I've found hollow shaft designs provide a noticeable improvement in responsiveness due to reduced rotational mass.
Arc Magnets vs. Straight Magnets
Magnet shape affects performance characteristics:
- Straight magnets: Traditional design, easier to manufacture
- Arc magnets: Curved to match the bell circumference, potentially more efficient
Some manufacturers claim 5-10% efficiency improvements with arc magnets, though real-world benefits vary.
Wire Gauge and Winding Techniques
Winding specifications affect performance:
- Wire gauge: Thicker wire (lower gauge number) handles more current but fewer turns fit in the stator
- Winding technique: Hand-wound vs. machine-wound affects consistency and performance
- Fill factor: How efficiently space in the stator is utilized by copper
Premium motors often advertise "high-density windings" with better fill factors, resulting in more copper mass and better performance.
Installation and Setup
Proper installation is crucial for optimal motor performance and longevity.
Proper Mounting Techniques
When mounting motors:
- Use appropriate screws - Too long can contact windings, too short won't secure properly
- Apply thread locker - Medium strength (blue) thread locker prevents vibration loosening
- Check for binding - Ensure the bell rotates freely after mounting
- Verify alignment - Motors should be perfectly perpendicular to the arms
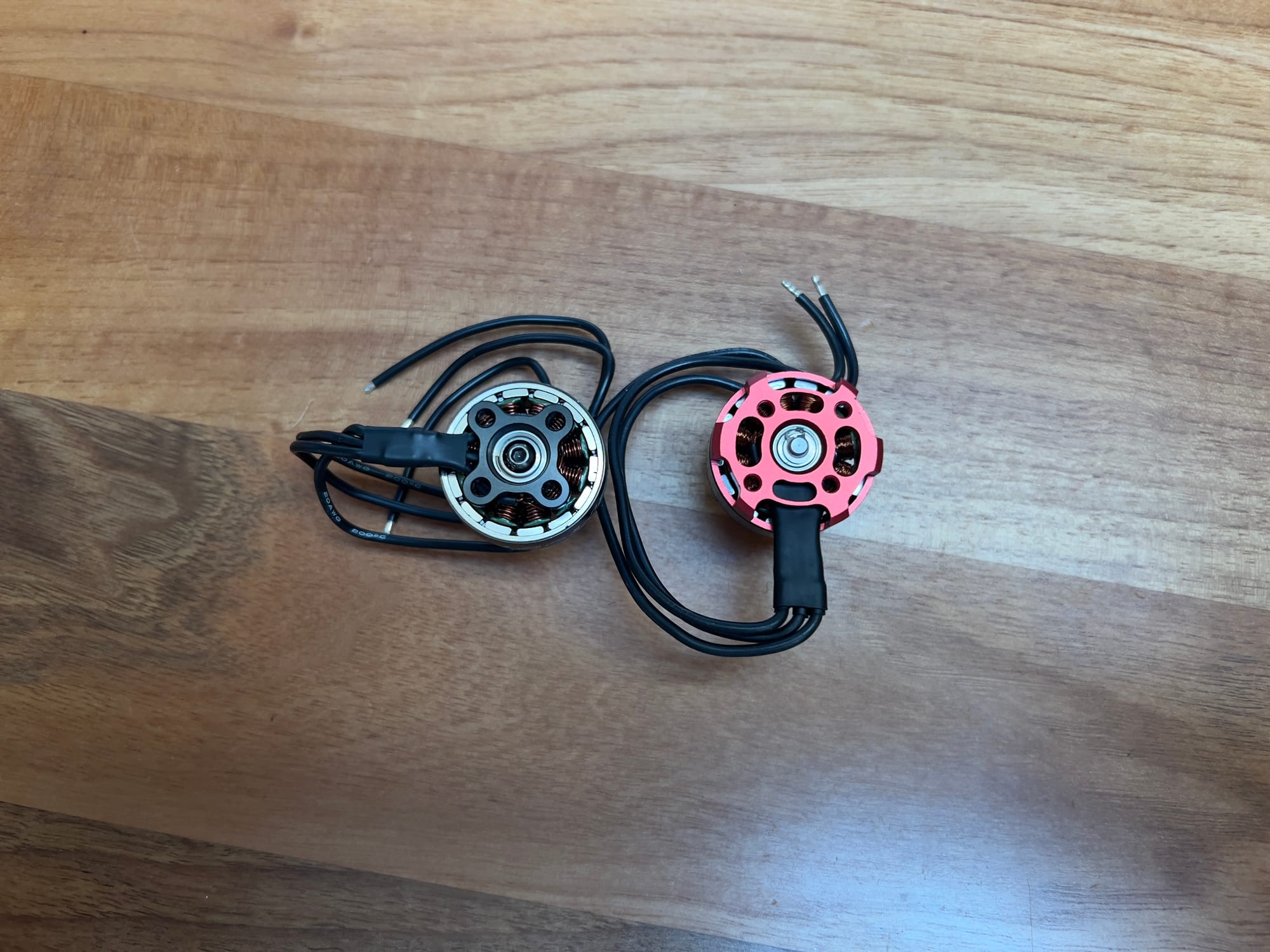
I learned the importance of proper mounting the hard way after losing a motor mid-flight due to vibration-loosened screws. Now I check motor mounting before every flying session.
Wire Management
Proper wire routing prevents damage and interference:
- Trim to appropriate length - Excess wire adds weight and can catch on obstacles
- Route away from props - Even with prop guards, wires can be cut
- Secure to frame - Prevent vibration and movement
- Consider ESC location - Shorter motor wires reduce resistance and weight
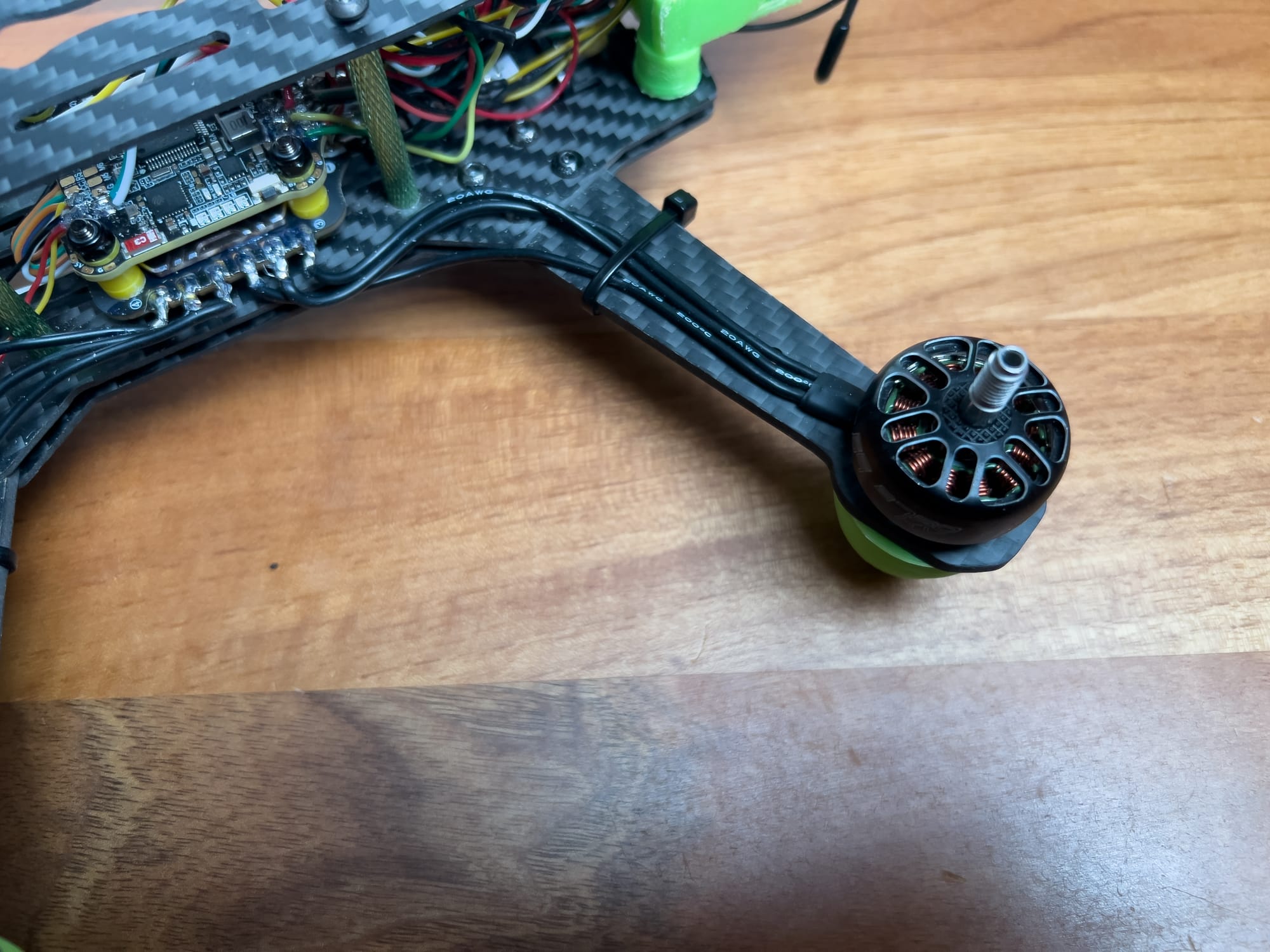
Motor Direction and Prop Orientation
FPV quads typically use a "props-in" or "props-out" configuration:
- Props-in: Props rotate inward at the front of the quad
- Better handling in forward flight
- More efficient in forward flight
- Standard for racing
- Props-out: Props rotate outward at the front
- Better yaw authority
- Reduced prop wash effect
- Popular for freestyle
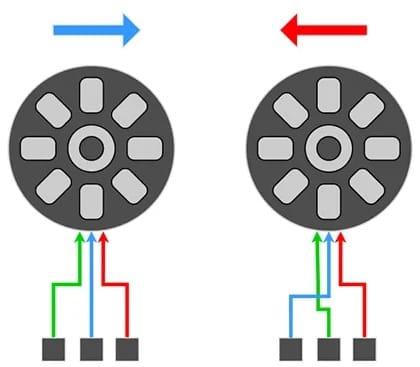
Motor direction is set in the flight controller software and by wire connection order to the ESC.
ESC Matching Considerations
Motors and ESCs should be matched for optimal performance:
- Current rating: ESCs should be rated for at least the motor's maximum current draw
- Response speed: Higher-quality ESCs provide faster, more precise motor control
- Protocol support: Modern ESCs should support DShot600 or higher for best performance
- Telemetry capability: ESCs with telemetry provide valuable data on motor performance
Soldering Best Practices
Good soldering is essential for reliable power delivery:
- Use adequate heat - 350-380°C for standard soldering irons
- Pre-tin wires and pads - Makes final connection easier
- Use quality solder - 60/40 or 63/37 leaded solder works best for motor connections
- Keep joints clean - Avoid excess solder that could cause shorts
- Use appropriate wire gauge - 20AWG is standard for 5" quad motors, 18AWG for larger builds
Poor soldering is one of the most common causes of performance issues and failures I've seen. I once spent hours troubleshooting erratic behavior that turned out to be a single cold solder joint on a motor wire.
Maintenance and Troubleshooting
Proper maintenance extends motor life and prevents failures.
Bearing Maintenance
Bearings are usually the first component to fail:
- Regular cleaning - Remove dust and debris after flying in dirty conditions
- Proper lubrication - A tiny drop of lightweight oil can extend bearing life
- Avoid water exposure - Dry thoroughly if motors get wet
- Listen for changes - Increased noise often indicates bearing wear
I've revived countless "dead" motors by simply replacing bearings—a skill worth learning if you're serious about the hobby.
Identifying Damaged Motors
Common signs of motor damage include:
- Physical damage: Bent shafts, cracked bells, or damaged windings
- Electrical issues: Shorts between phases or to ground
- Performance problems: Reduced power, excessive heat, or vibration
- Unusual sounds: Grinding, clicking, or inconsistent noise
Common Failure Points
Understanding typical failure modes helps with prevention:
- Bearings - Usually the first component to fail
- Windings - Can be damaged by overheating or physical impact
- Magnets - Can crack, shift, or demagnetize from impacts or excessive heat
- Shaft - Can bend from crashes or hard landings
- Bell - Can crack or become imbalanced from impacts
Debris Removal and Cleaning
Regular maintenance prevents issues:
- Remove visible debris - Check for hair, string, or plant material wrapped around the bell
- Compressed air cleaning - Blow out dust and small particles
- Check for contamination - Look for oil or dirt on windings
- Inspect for corrosion - Particularly after flying near saltwater
Shaft Straightening Techniques
Slightly bent shafts can sometimes be salvaged:
- Identify the bend - Roll the motor on a flat surface to find the high point
- Gentle pressure - Use a motor tool or pliers with protection to apply gentle pressure
- Test frequently - Check progress often to avoid over-correction
- Know when to replace - Some bends are too severe to fix reliably
I've successfully straightened many motor shafts, but it's a delicate process—too much force will make the problem worse.
When to Repair vs. Replace
Guidelines for decision-making:
- Replace if:
- Windings are damaged
- Multiple magnets are loose or damaged
- Shaft is severely bent
- Bell is cracked or significantly damaged
- Consider repair if:
- Only bearings are worn
- Shaft is slightly bent
- Single magnet is loose but undamaged
- Performance issues are minor
Pro Tips and Expert Insights
After years of building, racing, and repairing drones, I've gathered some insights that go beyond the specifications.
Fine-tuning Motor Performance
- Balance your props - Even factory props benefit from balancing
- Check and eliminate vibrations - They reduce performance and cause premature wear
- Consider motor timing - Adjusting ESC timing can fine-tune motor response
- Match motors carefully - Use motors from the same batch for best results
- Break-in period - Some motors perform better after a few flights to seat bearings
Custom Modifications
For those willing to experiment:
- Bearing upgrades - Replacing stock bearings with premium options
- Custom bell modifications - Some pilots drill strategic cooling holes
- Shaft upgrades - Titanium replacement shafts for durability
- Custom balancing - Beyond factory balance for maximum performance
- Winding modifications - Advanced users can rewind motors for specific characteristics
Racing Secrets
Competitive racers often:
- Undertilt motors - Slightly tilting motors back improves forward flight efficiency
- Use lighter bells - Sacrificing some durability for responsiveness
- Run motors at the edge - Accepting shorter lifespan for maximum performance
- Match motors to tracks - Different motors for technical vs. high-speed tracks
- Desync tuning - Carefully adjusting ESC parameters to prevent desync issues
Longevity Optimization
For maximum motor life:
- Stay below 80% throttle for most flying
- Allow cooling time between aggressive flights
- Check temperatures regularly
- Inspect and clean after crashes
- Store with care - Avoid humidity and extreme temperatures
Future Motor Technology Trends
Looking ahead, we can expect:
- Further integration - Combined motor/ESC/prop systems
- Smart motors with integrated sensors and telemetry
- New materials for lighter weight and better heat dissipation
- Increased efficiency through design and material improvements
- Specialized designs for emerging drone categories
FAQ: Common Questions About Drone Motors
How do I know what size motors to use for my drone?
Start with the frame size and intended use. For a standard 5" freestyle quad, 2207 or 2306 motors are excellent all-rounders. For racing, consider slightly smaller 2205 or 2206 motors. For micro builds under 3", look at 1303-1404 size motors. Match the motor to both the frame size and your flying style—racing needs higher KV, freestyle benefits from medium KV, and long-range/cinematic builds work best with lower KV motors.
What does motor KV actually mean?
KV (Kilo-Velocity) represents the theoretical RPM (revolutions per minute) a motor will turn per volt applied with no load. A 2400KV motor powered by a 4S battery at 16.8V (fully charged) would theoretically spin at 40,320 RPM without a propeller. In practice, the actual RPM will be lower due to the load of the propeller and other inefficiencies. Higher KV means faster rotation but less torque, while lower KV provides more torque but slower maximum rotation.
How important are motor bearings?
Extremely important—bearings are usually the first component to fail in a motor. Quality bearings provide smoother operation, better efficiency, and much longer lifespan. If your motors develop a grinding sound or feel rough when you spin the bell by hand, the bearings are likely wearing out. For serious pilots, upgrading to Japanese or European bearings can significantly improve motor longevity.
Can I mix different motors on the same drone?
While it's technically possible, it's not recommended. Different motors, even of the same size and KV, can have slightly different performance characteristics. This can create handling imbalances and make tuning difficult. If you must replace a single damaged motor, try to get the exact same model from the same production batch if possible.
How do I know if my motors are the right size for my build?
After a flight, check the motor temperature. They should be warm but not too hot to touch (ideally under 60°C). If they're extremely hot, your motors might be undersized for your build or you're using too aggressive props. Also, look at your hover throttle position—ideally, your drone should hover at around 30-40% throttle. If you need significantly more throttle to hover, your motors might be undersized or underperforming.
What's more important, motor size or KV rating?
Both are important but serve different purposes. Motor size (stator dimensions) determines the power potential and torque, while KV determines how that power is delivered in terms of RPM vs. torque. For a given battery voltage, higher KV means more RPM but less torque, while larger stator size means more overall power capability. Match both to your specific requirements—a freestyle quad might use 2207 2300KV motors, while a long-range build might prefer 2507 1700KV motors.
How often should motors be replaced?
With proper care, quality motors can last hundreds of flights. Replace motors when:
- Bearings become noisy or rough even after maintenance
- Performance noticeably decreases
- Windings are damaged
- Shaft becomes bent beyond repair
- Bell is cracked or damaged
- Magnets become loose or damaged
Many issues can be fixed with bearing replacements, which is much more economical than replacing the entire motor.
Do expensive motors really perform better than budget options?
In many cases, yes, but with diminishing returns. The jump from budget ($10) to mid-range ($20) motors usually brings significant improvements in performance, consistency, and reliability. However, the difference between mid-range and premium ($30+) motors is often more subtle and may only be noticeable to experienced pilots or in competitive scenarios. For most hobbyists, mid-range motors from reputable manufacturers offer the best value proposition. I've found that the sweet spot is typically in the $18-25 range, where you get most of the performance benefits without the premium price tag.
How can I tell if a motor is damaged after a crash?
After a crash, perform these checks:
- Spin the bell by hand - it should rotate smoothly without grinding or catching
- Check for physical damage to the bell, shaft, or base
- Look for exposed windings or signs of wire damage
- Ensure the shaft is straight by rolling it on a flat surface
- Check that all magnets are secure and in place
- Test the motor with very low throttle inputs before flying
Even if a motor passes these checks, monitor it closely during your next flight. Unusual vibrations, heat, or noise can indicate hidden damage.
What's the difference between "N" and "P" versions of motors?
Some manufacturers offer normal ("N") and power ("P") versions of the same motor. The "P" versions typically have more aggressive winding configurations designed for maximum power output, often at the expense of efficiency. They're intended for racing and extreme freestyle where maximum thrust is prioritized over flight time. For most pilots, the standard "N" versions provide a better balance of performance and efficiency.
Conclusion
Selecting the right motors for your FPV drone is one of the most consequential decisions in the build process. The perfect motor isn't necessarily the most powerful or the most expensive—it's the one that best matches your specific requirements, flying style, and the rest of your components.
For beginners, I recommend starting with mid-range motors in standard sizes (2306 or 2207 with 1800-2300KV for 5" freestyle quads) from reputable manufacturers. As you develop your skills and preferences, you can experiment with more specialized options tailored to your evolving flying style.
Remember that motor performance is just one part of a complex system. The best motors won't perform well with mismatched props, inadequate ESCs, or poor tuning. Take a holistic approach to your build, ensuring all components work harmoniously together.
The FPV motor landscape continues to evolve rapidly, with manufacturers constantly pushing the boundaries of what's possible in terms of power, efficiency, and reliability. By understanding the fundamental principles and specifications covered in this guide, you'll be well-equipped to navigate these changes and make informed decisions for your builds.
Whether you're building your first drone or your fiftieth, I hope this guide helps you find the perfect motors to match your flying dreams. Happy flying!
References and Further Reading
- Drone ESCs: Principles and Operation
- Drone Flight Controllers: Principles and Operation
- Overview of Drone Battery Types and Chemistry
- Drone Vibration Damping
External Resources
- Miniquad Test Bench - Comprehensive motor testing data
- Joshua Bardwell's YouTube Channel - Detailed motor explanations and tutorials
- eCalc Motor Calculator - Tool for estimating motor performance with different props and batteries
Comments ()