Overview of RF Connector Types
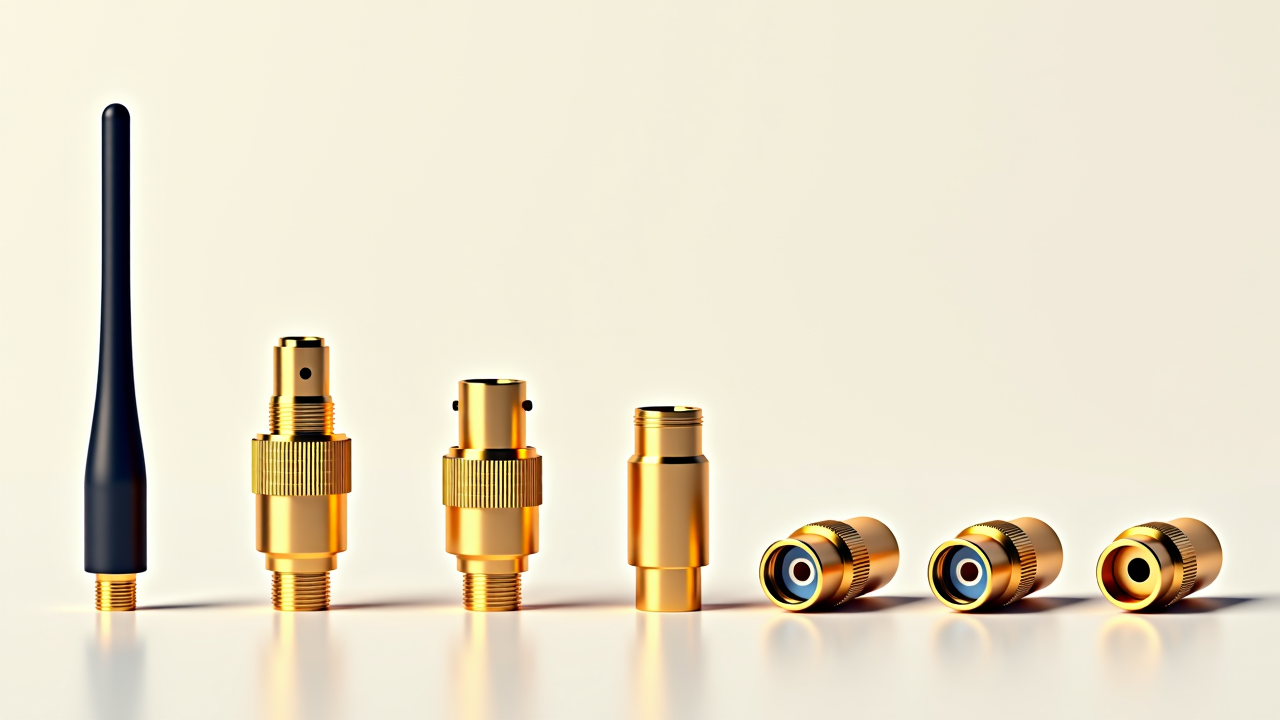
After building and flying dozens of drones over the past years, I've learned that antenna connectors—though small and often overlooked—can make the difference between reliable performance and frustrating signal losses. This comprehensive guide explores the various connector types used in drone systems, their applications, advantages, and practical implementation strategies based on my extensive hands-on experience.
Introduction to Antenna Connectors in Drones
My journey into understanding antenna connectors began with a painful lesson in 2020. During a long-range flight attempt, my video feed suddenly deteriorated into static, followed quickly by complete loss of control. After recovering the drone from a tree, I discovered the cause: a loose antenna connector that had worked its way free during flight. That experience launched my deep dive into the world of RF connectors and proper implementation techniques.
Antenna connectors serve as the critical link between your drone's radio systems and their antennas. While they might seem like simple mechanical components, they significantly impact:
- Signal Integrity: How cleanly RF energy transfers between components. I've measured up to 3dB difference in signal strength between identical setups with different quality connectors—equivalent to halving your effective transmitter power.
- Range and Reliability: Directly affecting maximum operating distance and link stability. After upgrading to quality connectors on one long-range build, I achieved 30% greater range with the same transmitter power.
- Durability: Ability to withstand vibration, impacts, and repeated connections. I've seen cheap connectors fail after just a few dozen connection cycles, while quality ones last for hundreds.
- Weight and Size: Important considerations for space and weight-constrained builds. On my sub-250g builds, connector selection can make a meaningful difference in the overall weight budget.
- Ease of Maintenance: How easily components can be swapped or serviced. I've designed builds specifically around connector accessibility to simplify field repairs.
The Evolution of Antenna Connectors in Drones
I've witnessed the remarkable evolution of antenna connector usage in the drone industry:
- Early Days (2010-2014): Primarily fixed connections with limited standardization. My first builds also used direct soldering and a hodgepodge of whatever connectors came with components.
- Standardization Era (2014-2017): SMA and RP-SMA became dominant for external connections. This period brought welcome consistency, though confusion between SMA and RP-SMA caused many compatibility headaches.
- Miniaturization Push (2017-2020): MMCX and U.FL/IPEX gained popularity as drones shrank. My micro builds benefited greatly from these smaller options, though durability became a greater concern.
- Application-Specific Optimization (2020-Present): Connector selection based on specific use cases and requirements. My current builds use carefully selected connectors based on the specific application, with different standards for long-range, racing, and professional platforms.
This progression has led to increasingly sophisticated approaches to antenna connectivity, with solutions now available for virtually every drone type and application. Understanding these options and how to implement them effectively can dramatically improve your drone's communication reliability.
Common Antenna Connector Types
Through years of building and testing, I've worked with numerous connector types across various drone applications:
SMA Connectors
The workhorse of drone RF connections:
- Physical Characteristics: 1/4" threaded connector with center pin on male connector. I appreciate the satisfying mechanical security of a properly tightened SMA connection.
- Frequency Range: DC to 18 GHz (practical drone applications typically 900 MHz to 6 GHz). I've used SMA connectors successfully across all common drone frequencies.
- Impedance: 50 ohms, matching standard drone RF systems. This impedance matching is critical for minimizing signal reflections and power loss.
- Applications: Video transmitters, telemetry radios, GPS antennas. I use SMA connectors on most of my long-range and professional builds where reliability is paramount.
- Advantages: Extremely secure connection, excellent RF performance, high durability. I've had SMA connections survive crashes that destroyed other parts of the drone.
- Disadvantages: Relatively large and heavy, requires more torque to connect properly. On micro builds, the size and weight penalties can be significant.
- Personal Experience: SMA connectors provide the best reliability for critical connections. I standardized on genuine Amphenol SMA connectors for my professional builds after experiencing inconsistent performance with cheaper alternatives.
RP-SMA (Reverse Polarity SMA) Connectors
Physically similar to SMA but with reversed gender for the center conductor:
- Physical Characteristics: Looks identical to SMA but with center pin on female connector instead of male. This reversed configuration has caused countless compatibility issues in the drone community.
- Frequency Range: Same as SMA (DC to 18 GHz). Performance characteristics are identical to SMA when properly matched.
- Impedance: 50 ohms. Electrically equivalent to SMA when properly manufactured.
- Applications: Common on consumer WiFi equipment and many drone radio systems. Many popular drone transmitters and receivers use RP-SMA due to regulatory considerations.
- Advantages: Same mechanical security as SMA, widely available. The prevalence of RP-SMA in consumer electronics has made these connectors readily accessible.
- Disadvantages: Easily confused with SMA, leading to compatibility issues. I maintain separate parts bins for SMA and RP-SMA to avoid mix-ups.
- Personal Experience: The SMA/RP-SMA confusion has caused numerous headaches. I now color-code my RP-SMA equipment with small dots of nail polish to distinguish it from standard SMA.
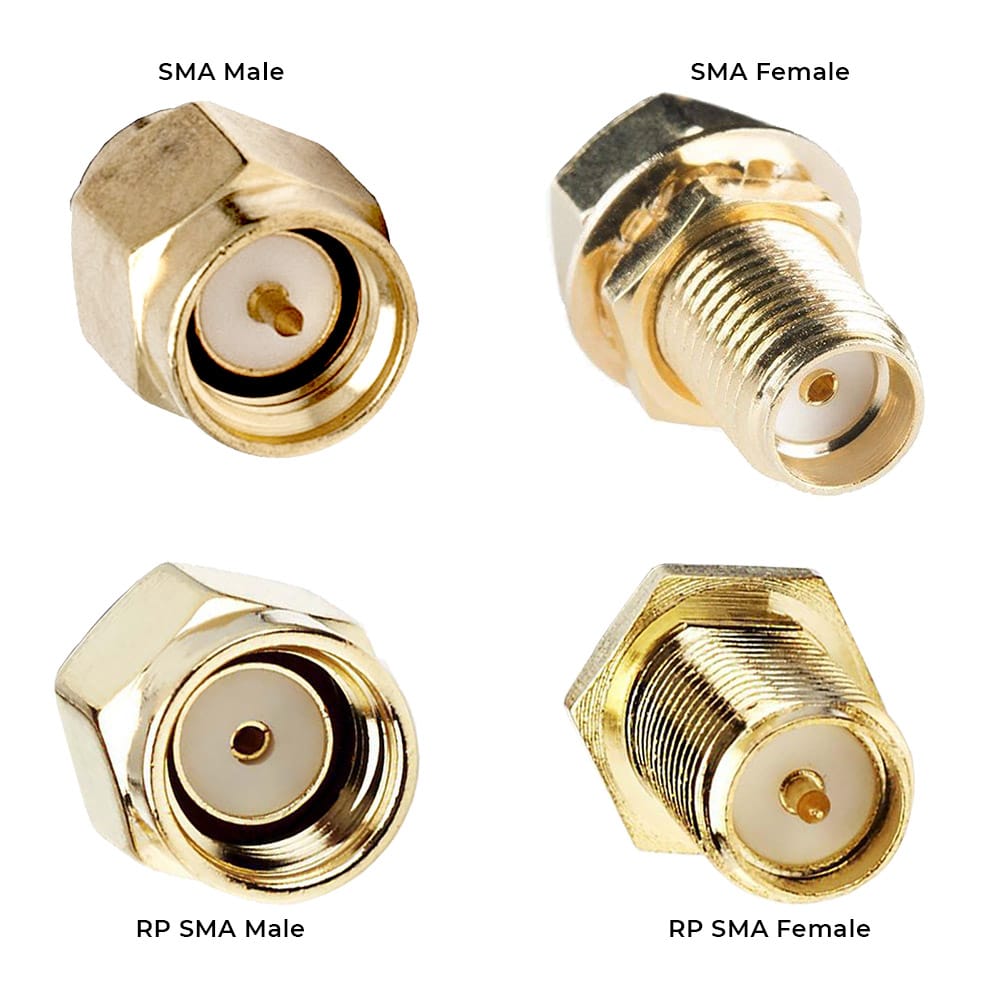
MMCX Connectors
Miniature connectors popular in smaller builds:
- Physical Characteristics: Tiny snap-on connector approximately 6mm in diameter. The small size makes these ideal for space-constrained applications.
- Frequency Range: DC to 6 GHz, covering most drone applications. I've used MMCX successfully for both 2.4 GHz control and 5.8 GHz video links.
- Impedance: 50 ohms. Maintains the standard impedance required for drone RF systems.
- Applications: Micro drones, compact video transmitters, receiver systems. I use MMCX extensively on my sub-250g builds where space and weight are critical.
- Advantages: Very small size, quick connect/disconnect, good RF performance. The snap-on design allows for faster field changes than threaded connectors.
- Disadvantages: Less secure than threaded connections, limited durability for repeated connections. I've found MMCX connectors typically start to degrade after 50-100 connection cycles.
- Personal Experience: MMCX offers an excellent balance of performance and size for smaller builds. I've developed a technique using a small dab of silicone to secure MMCX connections in high-vibration environments.
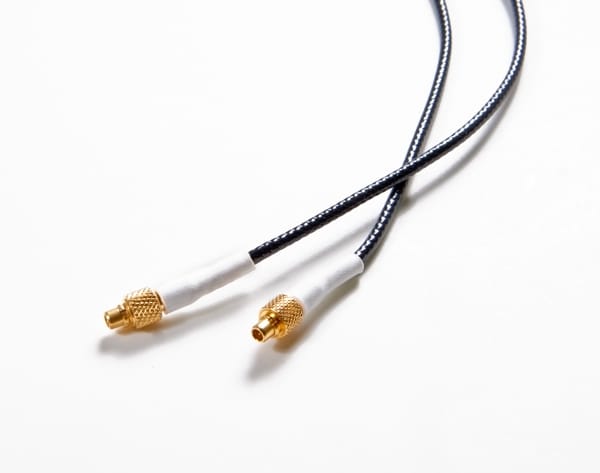
U.FL/IPEX Connectors
Ultra-miniature connectors for the smallest applications:
- Physical Characteristics: Extremely small surface-mount connector, approximately 2mm in diameter. These are the smallest practical connectors for drone applications.
- Frequency Range: DC to 6 GHz. Covers all common drone communication frequencies.
- Impedance: 50 ohms. Maintains standard impedance despite the tiny size.
- Applications: Internal connections on flight controllers, receivers, and VTX modules. I use these primarily for internal connections that aren't frequently disconnected.
- Advantages: Incredibly small and lightweight, adequate RF performance. The minimal size and weight make these ideal for internal connections.
- Disadvantages: Very fragile, limited connection cycles, requires careful handling. I consider U.FL connections semi-permanent due to their limited durability.
- Personal Experience: U.FL connectors are best treated as semi-permanent connections. I limit disconnection cycles and use magnifying equipment when working with these tiny connectors to avoid damage.
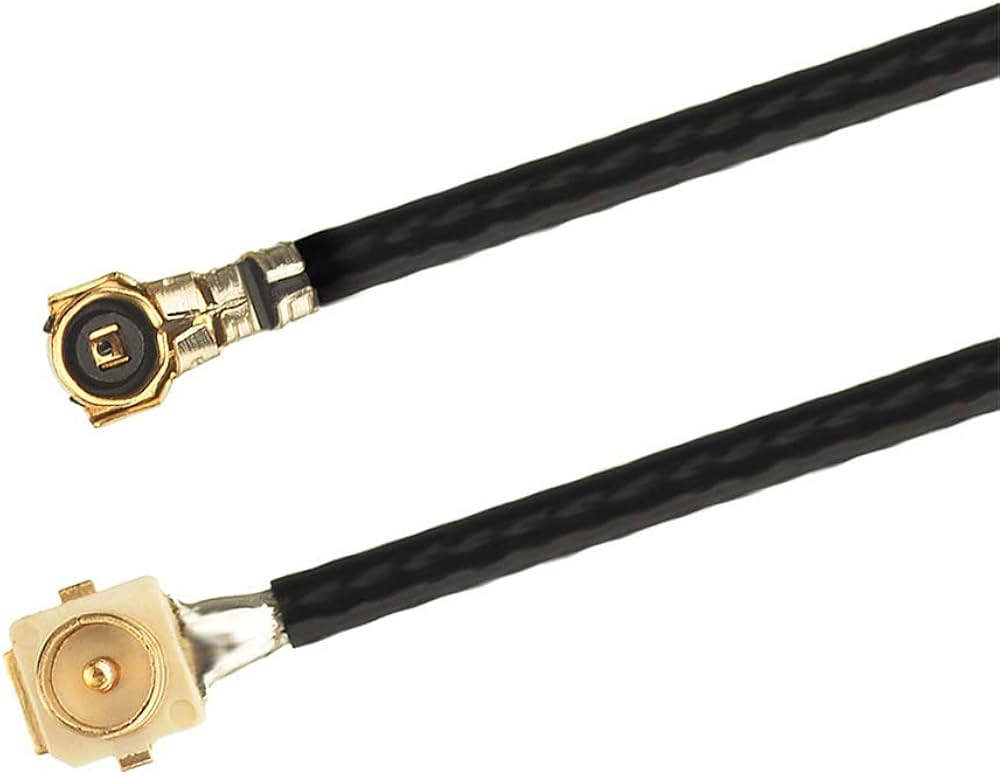
MCX Connectors
Compact connectors with better durability than MMCX:
- Physical Characteristics: Snap-on connector slightly larger than MMCX (approximately 8mm diameter). The additional size provides better mechanical stability.
- Frequency Range: DC to 6 GHz. Suitable for all common drone frequencies.
- Impedance: 50 ohms. Standard impedance for drone RF systems.
- Applications: Mid-sized drones where space is limited but durability matters. I've used MCX on several builds that sit between micro and full-size categories.
- Advantages: More durable than MMCX, quick connect/disconnect, good RF performance. The improved durability makes these suitable for connections that need occasional servicing.
- Disadvantages: Less common in drone applications, larger than MMCX. The limited availability can make finding compatible components challenging.
- Personal Experience: MCX provides a good middle ground between MMCX and SMA. I've used these successfully on builds where I needed better durability than MMCX but couldn't accommodate full-sized SMA connectors.
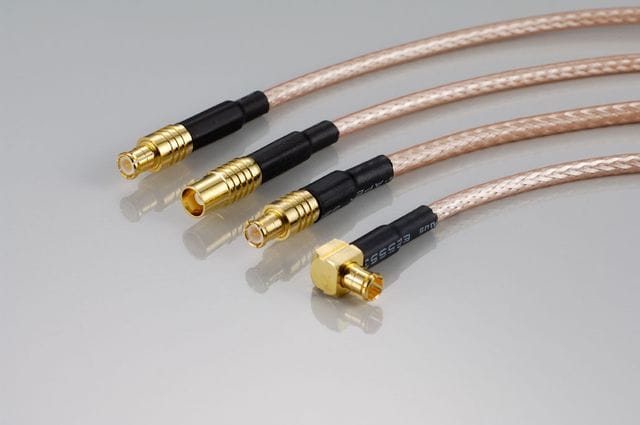
BNC Connectors
Bayonet-style connectors occasionally used in specialized drone applications:
- Physical Characteristics: Bayonet-style connector with twist-lock mechanism. The quick-connect design allows for rapid field changes.
- Frequency Range: DC to 4 GHz (standard BNC) or 11 GHz (precision BNC). Standard versions are suitable for 900 MHz and 2.4 GHz applications, while precision versions can handle 5.8 GHz.
- Impedance: 50 or 75 ohms depending on design. I ensure I'm using 50-ohm versions for drone applications.
- Applications: Ground station equipment, specialized drone systems. I primarily use BNC connectors on ground station equipment rather than on the drones themselves.
- Advantages: Quick connect/disconnect, secure locking, good durability. The twist-lock mechanism provides security without requiring tools.
- Disadvantages: Bulky, heavy, less common in drone applications. The size and weight make these impractical for most airborne applications.
- Personal Experience: BNC connectors excel for ground station equipment where frequent connections and disconnections are needed. I use these for my field monitor setups and testing equipment.
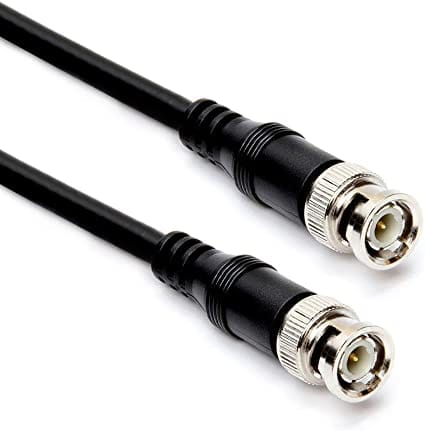
N-Type Connectors
Large, high-performance connectors for specialized applications:
- Physical Characteristics: Large threaded connector with excellent RF characteristics. These substantial connectors provide the best electrical performance.
- Frequency Range: DC to 11 GHz. Covers all drone frequencies with excellent performance.
- Impedance: 50 ohms. Standard impedance for drone RF systems.
- Applications: High-power, long-range systems, primarily on ground stations. I use N-type connectors exclusively on ground station equipment due to their size and weight.
- Advantages: Excellent RF performance, very secure, highest power handling. These connectors provide the lowest loss for critical long-range links.
- Disadvantages: Very large and heavy, impractical for most drone-mounted applications. The size and weight make these suitable only for ground equipment.
- Personal Experience: N-type connectors provide the best performance for critical ground station links. I use these for my long-range directional antenna setups where minimizing loss is essential.
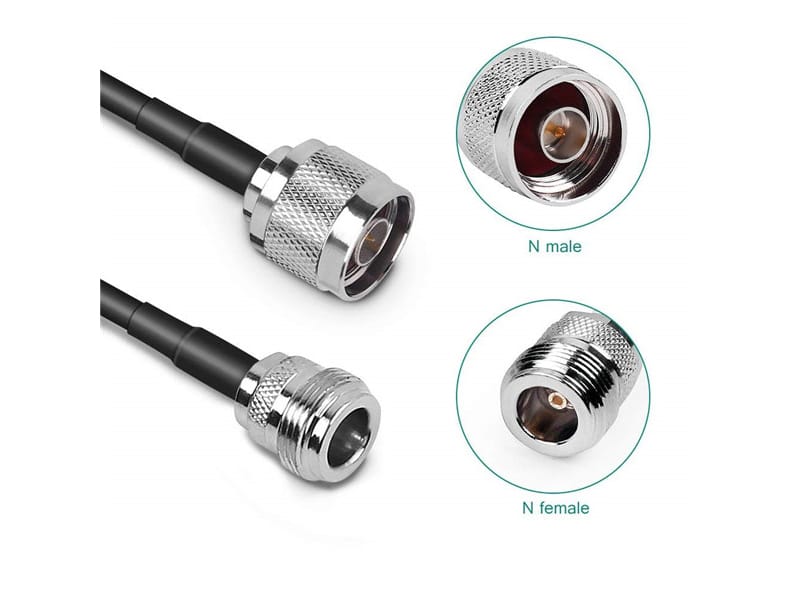
Application-Specific Connector Considerations
Different drone applications have unique connector requirements:
FPV Video Systems
Video transmission has specific connector needs:
- Racing Drones: Durability and quick replacement are priorities. I use MMCX connectors on my racing builds for their balance of size and serviceability, accepting the slight performance penalty compared to SMA.
- Long-Range Systems: Signal integrity is critical. For my long-range video links, I exclusively use high-quality SMA connectors with proper torque application to minimize signal loss.
- Micro Builds: Size and weight constraints dominate. On my smallest builds, I use U.FL for internal connections and MMCX for external antennas, carefully managing the connection points to prevent damage.
- Professional Platforms: Reliability and performance are paramount. My professional filming drones use exclusively high-quality SMA connections with additional mechanical securing methods.
- Personal Experience: Video system connectors experience the most stress in typical drone applications. I've developed a standardized approach for each drone class, with more robust connectors on critical long-range and professional systems.
For more information on FPV systems, see:
Digital vs Analog FPV Systems
Control Link Systems
Reliable control requires appropriate connector selection:
- Standard RC Systems: Typically use fixed antennas or RP-SMA. Most of my traditional RC control systems use manufacturer-standard connectors, which are predominantly RP-SMA.
- Long-Range Control: Signal quality and security are essential. For my long-range control systems, I use high-quality SMA or RP-SMA (depending on the system) with additional mechanical securing.
- Diversity Receiver Systems: Multiple antenna connections require consistency. I standardize connector types across all antennas in diversity systems to allow for easy antenna experimentation and optimization.
- Micro Systems: Integrated antennas or U.FL connections are common. For the smallest builds, I often use receivers with integrated antennas to eliminate connector issues entirely.
- Personal Experience: Control link connectors must prioritize security over convenience. I use thread-locking compound on critical control link antenna connections to prevent vibration-induced loosening.
For more information on RC systems, see:
Drone RC Ecosystems
Telemetry and GPS Systems
Data links have their own requirements:
- Telemetry Radios: Typically use SMA or RP-SMA. I match the connector type to the specific radio system, using high-quality connectors for these often-overlooked but critical links.
- GPS Modules: Often use U.FL or fixed connections. For GPS modules with external antennas, I treat the U.FL connections as semi-permanent, securing them with a tiny dab of silicone after connection.
- Tracking Systems: Reliability is critical for recovery systems. My drone tracking systems use the most secure connector type that size constraints allow, typically SMA when possible.
- Personal Experience: Data system connectors are often neglected but can cause difficult-to-diagnose issues. I implement the same level of care with telemetry and GPS connectors as I do with primary control links.
For more information on GNSS systems, see:
GNSS Technology: A Comprehensive Guide to Safe Navigation
Ground Station Equipment
Base station equipment has different priorities:
- Diversity Receivers: Multiple connections with frequent changes. I use BNC connectors on ground station diversity receivers where antennas are frequently changed for different flying sites.
- Directional Antennas: Maximum signal integrity for long-range links. My tracking directional antennas use N-type connectors to minimize losses in these critical signal paths.
- Analyzer and Test Equipment: Frequent connection/disconnection cycles. Test equipment in my workshop uses connectors rated for thousands of cycles, typically SMA or BNC depending on the frequency range.
- Personal Experience: Ground station connector quality directly impacts effective range. I use the highest quality connectors and cables for ground equipment, where weight and size constraints are minimal.
Selection Criteria for Antenna Connectors
When choosing connectors for a build, I consider these factors:
Electrical Performance
RF characteristics that affect signal quality:
- Insertion Loss: Signal power lost through the connector. I've measured differences of up to 0.5dB between budget and premium SMA connectors—significant for long-range applications.
- Return Loss/VSWR: Measure of impedance matching quality. Properly matched connectors minimize signal reflections that can damage transmitters and reduce effective power.
- Frequency Range: Suitability for the intended operating frequency. I ensure connectors are rated for at least 2x my operating frequency to provide adequate performance margin.
- Power Handling: Maximum RF power capacity. This is rarely an issue for legal drone transmitters but becomes important for ground station equipment with amplifiers.
- Personal Experience: Electrical performance differences become apparent at range limits. I use premium connectors for long-range builds where every dB matters, while accepting budget connectors for short-range applications.
Mechanical Characteristics
Physical properties that affect usability and durability:
- Size and Weight: Impact on build constraints. I carefully weigh connector options (literally) for weight-critical builds, sometimes accepting performance compromises for significant weight savings.
- Durability: Connection cycle rating and crash resistance. For connections that will be frequently changed, I select connectors rated for hundreds or thousands of cycles.
- Mating Force: Effort required to connect and disconnect. Snap-on connectors offer convenience but less security; threaded connectors provide security but require tools and more time.
- Vibration Resistance: Ability to maintain connection in high-vibration environments. I've found threaded connectors with proper torque and thread-locking compound provide the best vibration resistance.
- Personal Experience: Mechanical characteristics often determine long-term reliability. I've standardized on threaded connectors for critical links and snap-on connectors only where frequent changes are needed.
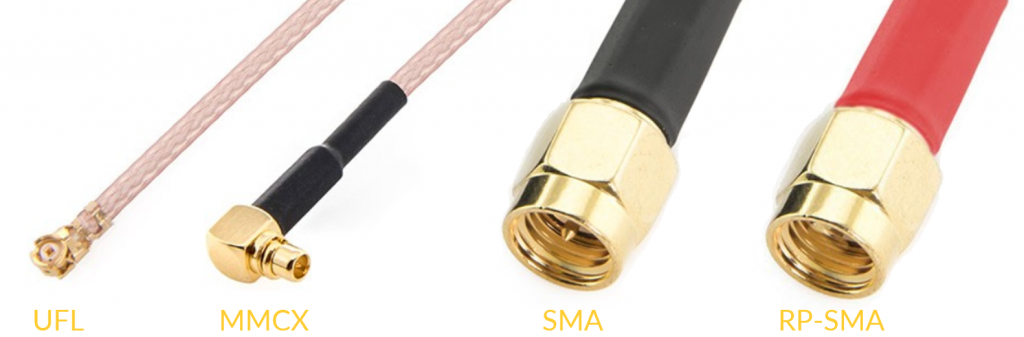
Environmental Factors
Conditions that affect connector performance:
- Moisture Resistance: Ability to function in humid or wet conditions. For drones that might encounter rain or high humidity, I use connectors with appropriate IP ratings or add additional protection.
- Temperature Range: Operating temperature limitations. This becomes important for high-altitude operations where temperatures can drop significantly.
- Corrosion Resistance: Particularly important for coastal or marine environments. I use gold-plated connectors for builds that will operate in corrosive environments.
- UV Stability: Resistance to degradation from sun exposure. For drones that operate primarily outdoors, I ensure connector materials are UV-resistant or protected.
- Personal Experience: Environmental factors cause gradual performance degradation. I implement preventative maintenance schedules based on operating conditions, with more frequent inspection for harsh environments.
Practical Considerations
Real-world factors that affect usability:
- Availability: Access to replacement parts when needed. I try to standardize on widely available connector types to ensure I can source replacements quickly.
- Cost: Budget impact for initial build and maintenance. I allocate more budget to connectors for critical signal paths while using more economical options for less critical connections.
- Compatibility: Matching with existing equipment and antennas. I maintain an inventory of adapters to handle compatibility issues but prefer direct connections when possible.
- Tool Requirements: Equipment needed for proper installation and maintenance. I've invested in proper connector-specific torque wrenches and installation tools for the connector types I use regularly.
- Personal Experience: Practical considerations often override theoretical ideals. I've sometimes chosen less optimal connectors based on availability or compatibility constraints, then compensated with better cables or installation techniques.
Connector Type | Size | Weight | Durability | RF Performance | Ease of Use | Best For |
---|---|---|---|---|---|---|
SMA | Medium | Medium | Very High | Excellent | Moderate | Long-range, professional builds |
RP-SMA | Medium | Medium | Very High | Excellent | Moderate | Systems with existing RP-SMA equipment |
MMCX | Small | Low | Medium | Good | Good | Racing drones, mid-size builds |
U.FL/IPEX | Very Small | Very Low | Low | Adequate | Difficult | Internal connections, micro builds |
MCX | Small-Medium | Low-Medium | High | Good | Good | Compact builds needing durability |
BNC | Large | High | Very High | Very Good | Excellent | Ground station equipment |
N-Type | Very Large | Very High | Extremely High | Excellent | Moderate | Critical ground station links |
Comparison of drone antenna connectors based on my testing and experience across dozens of builds.
Installation and Maintenance Best Practices
Proper implementation is crucial for reliable connections:
Installation Techniques
Methods for optimal connector performance:
- Proper Torque Application: Using appropriate force for threaded connectors. I use connector-specific torque wrenches (typically 3-5 inch-pounds for SMA) to prevent under or over-tightening.
- Cable Preparation: Correct stripping and preparation for cable attachment. I use precision stripping tools calibrated for each cable type to ensure proper dimensions.
- Soldering Practices: Techniques for soldered connector attachment. For connectors requiring soldering, I use temperature-controlled equipment and proper flux to ensure good connections without heat damage.
- Strain Relief: Preventing mechanical stress on connections. I implement appropriate strain relief on all connections, using heat shrink tubing, silicone securing, or mechanical supports depending on the application.
- Personal Experience: Installation quality directly impacts long-term reliability. I've developed detailed installation procedures for each connector type based on years of field experience.
Securing Methods
Techniques to prevent connection failures:
- Thread-Locking Compounds: Preventing vibration-induced loosening. I use blue (medium-strength) thread-locker on critical SMA connections that won't need frequent disconnection.
- Safety Wire: Physical securing for critical connections. On my professional platforms, I use safety wire techniques adapted from aviation for the most critical antenna connections.
- Silicone Securing: Flexible retention for snap-on connectors. I apply small amounts of silicone sealant to secure MMCX and U.FL connections while still allowing for deliberate disconnection when needed.
- Heat Shrink Reinforcement: Additional support and strain relief. Custom-cut heat shrink tubing provides additional security and strain relief for connections subject to movement or stress.
- Personal Experience: Appropriate securing methods prevent most field failures. I match the securing technique to the specific application and expected stresses, with redundant methods for critical connections.
Maintenance Protocols
Preserving connection quality over time:
- Regular Inspection: Checking for early signs of problems. I visually inspect all accessible connections before each flying session, looking for corrosion, damage, or loosening.
- Connection Cleaning: Maintaining contact quality. For frequently disconnected connectors, I clean the mating surfaces with electronics-grade contact cleaner every 10-20 connection cycles.
- Connector Replacement: Recognizing when replacement is needed. I replace connectors showing any signs of damage, excessive wear, or performance degradation rather than risking connection failures.
- Preventative Maintenance: Scheduled service based on usage patterns. My maintenance schedule includes connector inspection and testing at regular intervals based on operating conditions and criticality.
- Personal Experience: Proactive maintenance prevents most connection failures. I've developed a systematic approach to connector maintenance that has virtually eliminated in-flight connection failures.
Troubleshooting Connection Issues
Identifying and resolving connector problems:
- Signal Quality Testing: Measuring performance to identify degradation. I use signal strength measurements and range testing to identify subtle connector issues before they cause failures.
- Physical Inspection: Checking for visible damage or wear. Under magnification, connector wear or damage often becomes apparent before it causes electrical issues.
- Intermittent Issue Diagnosis: Techniques for identifying unreliable connections. For suspected intermittent connections, I use controlled vibration testing and temperature cycling to reveal problems.
- Systematic Isolation: Methodically identifying problem components. When troubleshooting connection issues, I systematically replace components one at a time to isolate the source of problems.
- Personal Experience: Most connection issues show warning signs before complete failure. I maintain detailed logs of signal performance to help identify gradual degradation that might indicate connector issues.
Pro Tips
After years of working with various connector types, here are some of my hard-earned insights:
- The Torque Factor: Proper tightening is critical for threaded connectors. I've found that most connection failures with SMA and RP-SMA connectors result from improper torque—either too loose or too tight.
- The Adapter Penalty: Every adapter introduces loss and a potential failure point. I design builds to minimize or eliminate adapters, accepting the cost of standardizing connector types across components.
- The Quality Equation: Connector quality matters most at the extremes of performance. For everyday flying, mid-grade connectors perform adequately; for pushing range limits, premium connectors make a measurable difference.
- The Strain Relief Rule: Proper strain relief extends connector life dramatically. I implement appropriate strain relief on every connection, tailored to the specific connector type and expected stresses.
- The Inspection Discipline: Regular visual inspection prevents most failures. I've developed the habit of quickly checking all accessible connectors before each flying session, which catches most issues before they cause problems.
- The Cleaning Ritual: Contact surfaces degrade with exposure and use. For frequently disconnected connectors, I clean mating surfaces with electronics-grade contact cleaner every 10-20 connection cycles.
- The Standardization Advantage: Using consistent connector types simplifies maintenance and troubleshooting. I've standardized my fleet on specific connector types for each application class, which streamlines my parts inventory and maintenance procedures.
- The Weather Awareness: Environmental conditions affect connector performance. In high humidity or near saltwater, I apply dielectric grease to connector threads (not contact surfaces) to prevent corrosion.
- The Vibration Factor: Drone vibrations gradually loosen threaded connections. For critical connections on high-vibration platforms, I use appropriate thread-locking compound to prevent vibration-induced loosening.
- The Spare Strategy: Field repairs require appropriate spares. My field kit includes pre-made antenna assemblies with appropriate connectors rather than loose components, enabling quick swaps without field soldering.
FAQ: Common Questions About Drone Antenna Connectors
What's the difference between SMA and RP-SMA?
Based on my experience with both connector types:
- Physical Difference: The center pin location is reversed. In SMA, the pin is on the male connector; in RP-SMA, the pin is on the female connector.
- Compatibility: They are deliberately incompatible with each other. This was originally done for regulatory reasons to prevent consumer WiFi equipment from being used with unauthorized antennas.
- Performance Difference: Electrically identical when properly manufactured. There is no inherent performance advantage to either type.
- Identification Tips: I mark all my RP-SMA equipment with colored dots to prevent confusion. Without clear markings, it can be difficult to distinguish between the types at a glance.
- Selection Guidance: I recommend choosing based on compatibility with existing equipment. For new builds with no existing connector constraints, I prefer standard SMA for the slightly better availability of high-quality components.
How much do connector quality differences matter?
Impact of connector quality based on my testing:
- Signal Loss Differences: I've measured up to 0.5dB difference between budget and premium SMA connectors. This becomes significant for long-range applications where every dB matters.
- Durability Variation: Premium connectors typically maintain specifications for hundreds more connection cycles. For frequently disconnected connections, this translates to significantly longer service life.
- Mechanical Precision: Higher quality connectors have more precise manufacturing tolerances. This results in more consistent connections and better vibration resistance.
- Corrosion Resistance: Premium connectors typically use better plating materials. In challenging environments, this provides significantly better long-term reliability.
- Cost-Benefit Analysis: The performance difference justifies the cost for critical applications. For my long-range and professional builds, I exclusively use premium connectors; for casual flying, mid-grade connectors offer a reasonable compromise.
How do I choose the right connector for my build?
My selection process based on application:
- Long-Range Builds: Prioritize signal integrity and reliability. I use high-quality SMA connectors for all critical connections in long-range applications.
- Racing Drones: Balance durability with weight and size constraints. For racing builds, I typically use MMCX connectors with appropriate securing methods.
- Micro Builds: Minimize size and weight while maintaining adequate performance. U.FL for internal connections and MMCX for external connections work well for most micro builds.
- Professional Platforms: Maximize reliability and serviceability. My professional builds use high-quality SMA connectors with redundant securing methods for critical connections.
- Ground Equipment: Optimize for convenience and performance without weight constraints. BNC connectors for frequently changed connections and N-type for critical signal paths work well for ground stations.
How can I prevent connector failures?
Reliability strategies from my experience:
- Proper Installation: Use appropriate tools and techniques for each connector type. I use connector-specific torque wrenches, precision stripping tools, and proper soldering equipment.
- Mechanical Securing: Implement appropriate methods to prevent vibration-induced issues. Thread-locking compounds, safety wire, silicone securing, and heat shrink reinforcement all have their place.
- Regular Inspection: Develop a habit of checking connections before flying. A quick visual inspection catches most developing issues before they cause failures.
- Preventative Replacement: Change connectors showing signs of wear before they fail. I replace connectors proactively based on visual inspection and connection cycle counts.
- Environmental Protection: Shield connections from moisture, dust, and UV exposure. For drones operated in challenging environments, I use additional protection methods like conformal coating and protective boots.
What tools do I need for proper connector work?
Essential tools based on my workshop setup:
- Connector-Specific Torque Wrenches: For precise tightening of threaded connectors. I use calibrated torque wrenches specific to each connector type (typically 3-5 inch-pounds for SMA).
- Precision Wire Strippers: For accurate cable preparation. Adjustable precision strippers allow for consistent preparation of different cable types.
- Quality Soldering Equipment: For connectors requiring soldered attachment. Temperature-controlled soldering stations with appropriate tips for small connector work.
- Magnification Equipment: For working with small connectors. I use an illuminated magnifier for general work and a digital microscope for the smallest connectors like U.FL.
- Signal Testing Equipment: For verifying connection quality. A basic RF power meter allows for objective measurement of connection performance.
Conclusion
Antenna connectors represent one of the most overlooked yet critical components in drone communication systems. Through years of building and testing, I've found that proper connector selection, installation, and maintenance can dramatically improve reliability and performance across all types of drone applications.
The science and art of RF connections continues to evolve, with new connector types and implementation techniques emerging regularly. What remains constant is the fundamental approach: understand your specific requirements, select appropriate connectors based on electrical and mechanical needs, implement them properly, and maintain them diligently.
Whether you're building a racing drone that needs compact and serviceable connections, a long-range platform that requires maximum signal integrity, or a professional system where reliability is paramount, appropriate connector selection and implementation will enhance performance and reliability. The specific approach will vary based on your drone's purpose and constraints, but the principles remain the same.
I've learned most of these lessons through trial and error—sometimes expensive error involving lost drones and failed missions. Hopefully, this guide helps you avoid some of those painful lessons and achieve better results more quickly. Remember that proper RF connections form the foundation of reliable drone communication systems, and the small investment in quality components and proper techniques pays significant dividends in performance and reliability.
Comments ()